Over five meters in length, almost one meter in diameter – a total of 9,700 kilograms of heat-resistant, quenched and tempered steel were machined at our Mönchengladbach works in such a way that one of the world's most powerful gas/steam turbines will soon be driven in the best possible way. So much detail work took time. It took six weeks for this impressive drive shaft to be completed.
This particular component is not part of the core business of the SMS group but is nevertheless part of the portfolio. As a well-known company in heavy-machine construction, particularly sophisticated steel workpieces have been manufactured here for a long time as order work for external companies. Customers include some of the world's largest companies.
"We are working here in 'Gladbach' with four stable columns," explains Joachim Gietmann, Head of the Mönchengladbach manufacturing center. "This means that we manufacture equipment for our three own business units Long Products, Forging Plants and Technical Service. And as a fourth pillar, we use our competence as an external service provider."
Mönchengladbach manufacturing center
The manufacturing center in Mönchengladbach was extensively modernized in 2015. In addition to the erection of a new assembly bay with an area of 4,000 square meters and 180 tons of crane capacity, 15 new machine tools were installed in the area of the previous machining shop. A machining center controlled by a central computer with fully automatic charging of workpieces and tools for individual weights of up to 10 tons, a boring mill line for machining cubic workpieces with individual weights of up to 120 tons, a gantry machine tool of up to 200 tons, as well as three five-axes turn/mill centers with maximum machining capacities for 60 tons workpiece weight and 20 meters workpiece length - these are key data of the manufacturing capacity.
The machining shop comprises modern tool technologies and has several CNC machining centers, turn-milling centers, plate boring machines with turning/shifting table and a gantry-type milling machine. Programming of the machines is by means of a 3D CAM system. Here, great importance is placed on the simulation of the complex machining processes for safeguarding trouble-free and faultless production. This leads to a reduction of errors and the associated cost savings.
Our Mönchengladbach site has two assembly bays with over 6,500 square meters of floor space for the Workshop Assembly department. Installation heights of up to 15 meters are possible thanks to two assembly pits. The scope of services also includes pipework and electrical equipment installation.
Test runs can also be carried out in the bays. Several test stands are available for this purpose. Each bay has a new crane with a capacity of up to 180 tons. In addition, 20 wall and gantry cranes for various weight classes ensure the assembly and installation work can progress without the need for waiting times. Loads of over 200 tons can be handled using the relevant lifting equipment.
Contract manufacturing at all locations
In addition to the production of core products and components of the SMS group product range, all workshops of the SMS group are also intended for contract manufacturing. The strengths lie in the following areas:
- Complex manufacturing of large parts
- Small series up to individual weights of 5 tons
- Mechanical drive components
- Complete gearboxes
- Hydraulic and pipe systems
- Installation of components for machine tools and for general plant and mechanical engineering
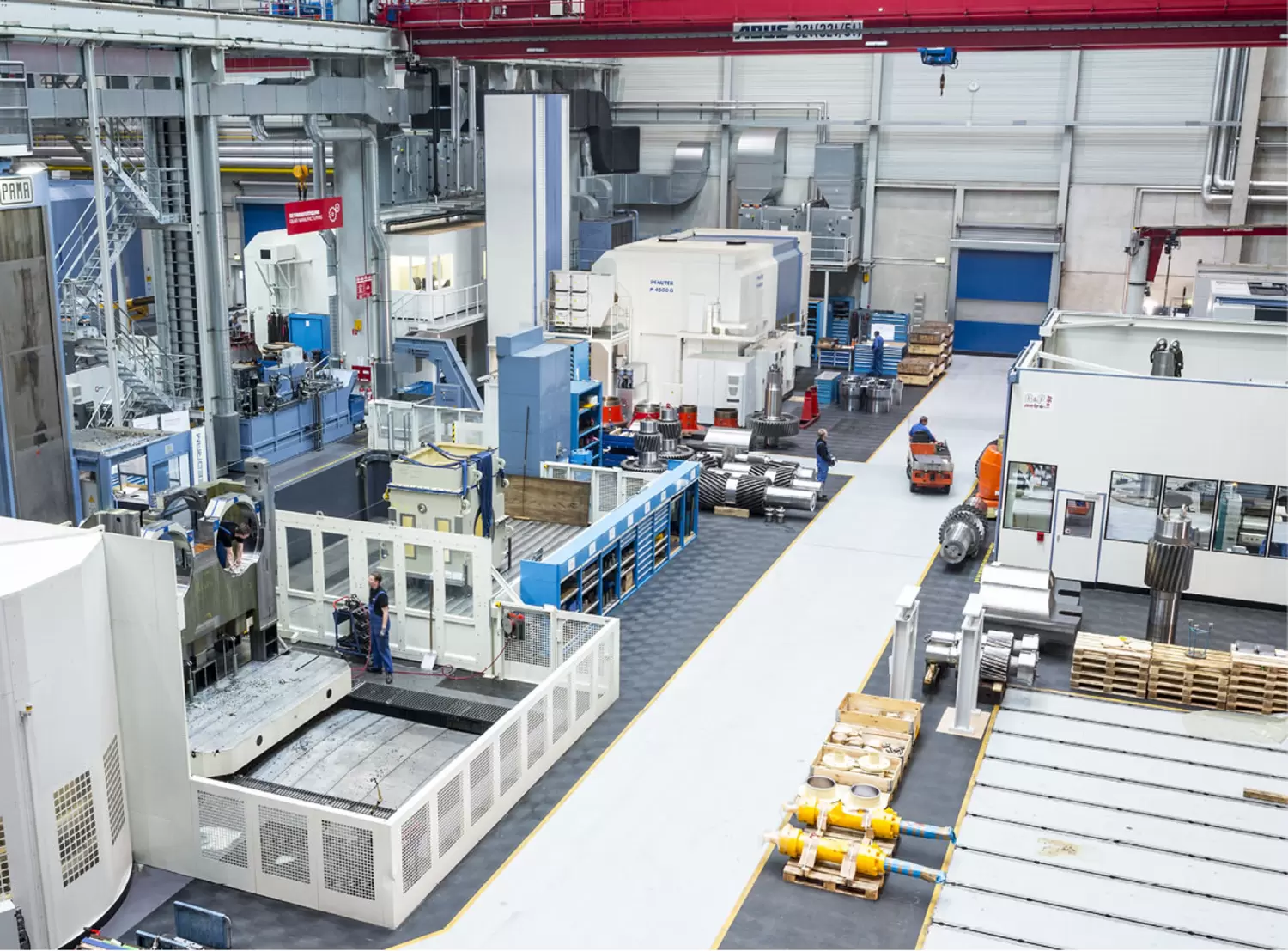
In the Mönchengladbach manufacturing center, around 10% of the machine capacity is today used for external orders. The demand is present: \"The quality and deadline requirements in the segment are extremely high. To fulfill both, you need a highly precise, ultra-modern machine park. A maximum depth of manufacture. And above all, of course, top-class qualified employees\", says Joachim Gietmann. Factors that all come together in Mönchengladbach.
Technical data of the turbine shaft for gas/steam turbines
- Diameter: 874 mm
- Length: 5,349 mm
- Weight: 9,700 kg
- Material: Heat-resistant, quenched and tempered steel 30CrMoNiV5-11+OT
- Cutting allowance of 5mm on the outer contour provided
- Finish-machining time: 6 weeks
Additional information
- Brochure: Manufacturing expertise worldwide
- Brochure: Machine park SMS group location Mönchengladbach