Ilsenburger Grobblech, a wholly-owned subsidiary of Salzgitter AG, has realized a project to increase occupational safety in the repair and service modes at a heavy-plate mill together with SMS group. The existing safety concept from the 1990s no longer met today’s requirements.
We are proud of the fact that people at Ilsenburger Grobblech GmbH always come first and consider safety at work in a holistic manner.
Christian Schön, Project Manager at Ilsenburger Grobblech: “We are proud of the fact that people at Ilsenburger Grobblech GmbH always come first and consider safety at work in a holistic manner. This means: we want to protect our staff not only in ongoing operations but also during maintenance work. For that reason, we made considerable investments.“
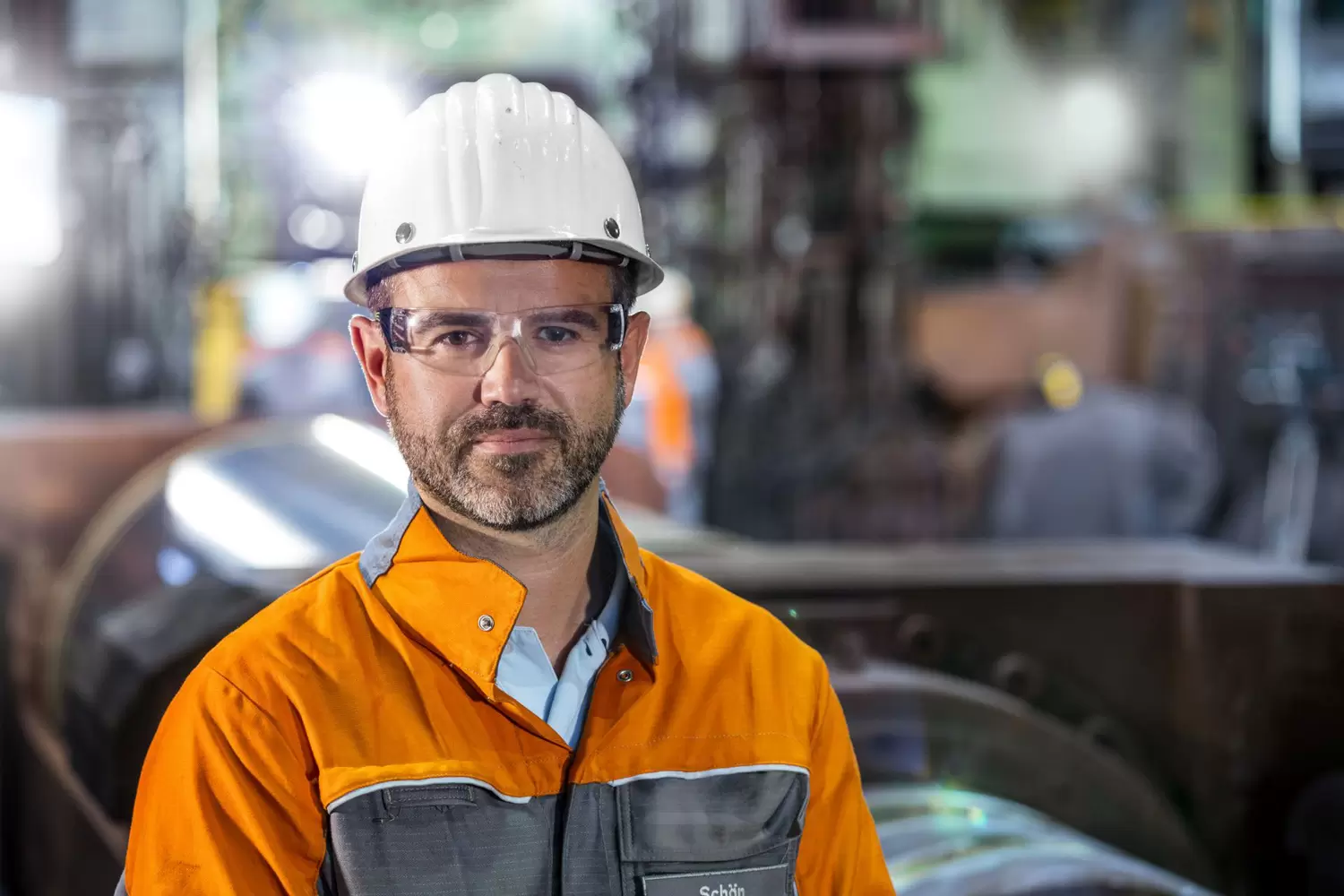
Risky procedure of replacing housing rolls
In the past, the replacement of housing rolls has always been particularly critical regarding repair and maintenance work. The rolls were fastened and lifted with steel wire ropes and disassembly was time-consuming and risky. In particular, communication via voice radio to the hydraulic cellar has been a weak point. All control commands for hydraulic operations during housing roll replacement had to be transmitted via voice radio and then manually adjusted in the hydraulic cellar. In the event that communication would have been disrupted maloperations could have been the result. Due to all of these uncertainties, the task was to develop a safe concept for replacing the housing rolls. “The annual replacement of the housing rolls which must be carried out by us due to wear is exemplary for an improvement and it becomes particularly evident how work operations in the maintenance mode can be enhanced,“ said Christian Schön.
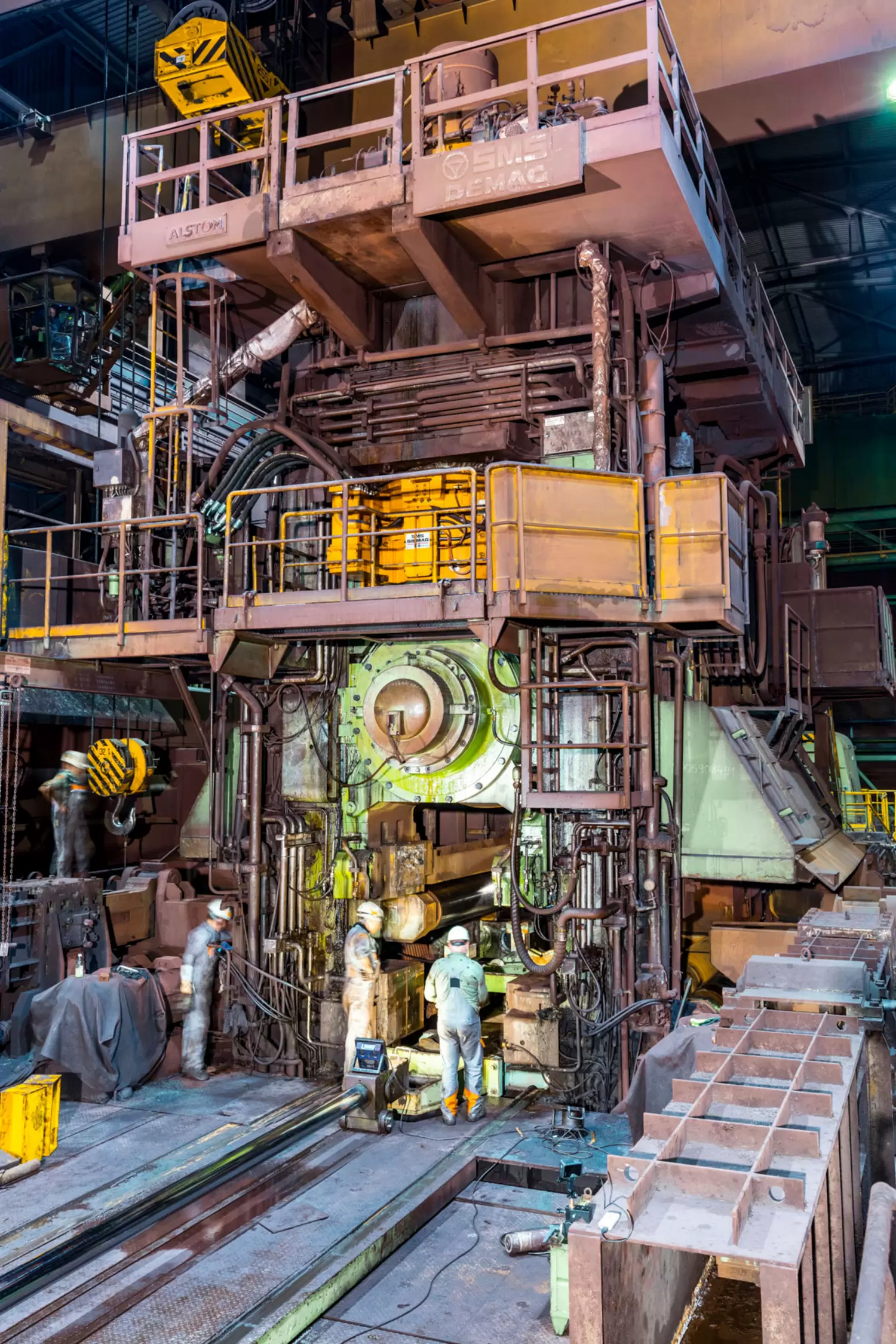
Three-stage plan for more safety
The basis for the modernization project was a three-stage plan realized during a period of three years.
- First stage: on-site investigations and analyses for risk assessment
- Second stage: joint development of safety concept
- Third stage: implementation of measures
The jointly developed solution by Ilsenburger Grobblech and SMS group encompasses new mechanical equipment such as four stepped levers at the top of the heavy-plate mill securing the backup roll balancing system in various positions. It comprised in addition new devices and drilled holes to insert modified T-head bolts instead of steel wire ropes. The optimization scope also includes the renewal of hydraulic components such as three new valve stands, a new tank with recirculation, the conversion on the existing equipment and the automation upgrade with new technologies, new functions and especially new safety controls.
The achievements demonstrated here can also be transferred to many older plants. Consequently, we are able to create maximum industrial safety in the repair and maintenance modes.
Interaction of solutions increases occupational safety
New and upgraded hydraulic equipment, new stepped levers and recent automation – all this interacts perfectly, now enabling safe repair and maintenance modes. The levers secure backup roll balancing for safe access during all servicing activities within the mill stand. The new positions secured by stepped levers are adapted optimally to various repair modes. The automation switches the entire mill stand to maintenance mode while all mechanical and hydraulic positions are safely monitored. Instead of a steel wire rope, the housing rolls are now lifted and retained by means of reliable T-head bolts. One of the most important innovations is the hydraulic control via radio remote control. All positions can be safely approached with the aid of a compact industrial radio control and maintenance specialists are no longer required in the hydraulic cellar. For disassembly and assembly, the entire maintenance team cooperates directly on the stand coordinating work operations in an optimal way. It is thus ensured that misunderstandings are prevented.
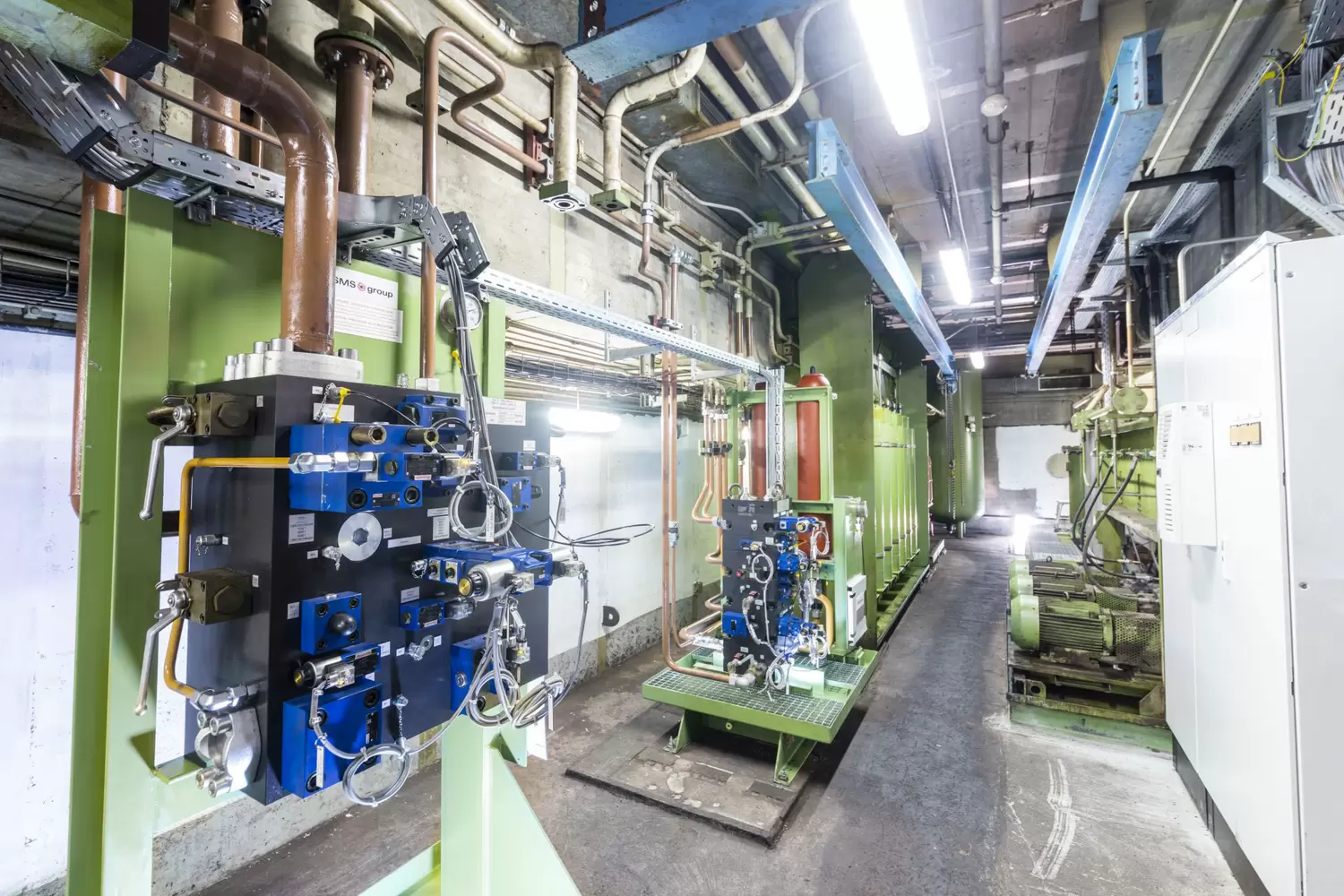
Reiner Stammberger, Project Manager at SMS group: “Blueprints do not exist for occupational safety in repair mode or maintenance work. Together with Ilsenburger Grobblech, we have developed customized solutions exactly tailored to the needs of these plants. The achievements demonstrated here can also be transferred to many older plants. Consequently, we are able to create maximum industrial safety in the repair and maintenance modes.“
Exemplary procedure
The procedure on valve stand No. 3 is exemplary for the execution of the project. Based on the analyses, the engineers of SMS group designed the new valve stand exactly according to these requirements. The digital design data were the basis to precisely manufacture the valve stand in the workshop of SMS group. Thereafter, comprehensive examinations took place in a modern valve test stand and the acceptance took place by experts of Ilsenburger Grobblech. Compared to the previous valve stand, the new stand is considerably more compact and nevertheless provides significantly more functions and more complex control options.
Only by renewing the hydraulic system and by implementing de-energizing circuits a reorganization of maintenance featuring safe functions could be realized. Interacting with the new automation, the new hydraulic system now enables a safe maintenance mode.
As regards how a high degree of occupational safety can be achieved in repair and maintenance modes, this project is a good example also for other companies.
Not only the safety standards were increased significantly, but also the availability of the heavy-plate mill was boosted since a replacement of the housing rolls can now be executed faster. “As regards how a high degree of occupational safety can be achieved in repair and maintenance modes, this project is a good example also for other companies“, concludes Reiner Stammberger.