Integrated strip guidance for improved rolling mill stability
During the hot rolling of steel strip interferences can occur when transporting the strip from one mill stand to the next mill stand. Such interferences may hinder the straight-line of the strip and produce a deviation from the centerline which cause ripped tails or even cobbles. The X-Pact® Centerline Control increases the rolling stability, reduces the number of unplanned roll changes and supports operator by suitable visualization.
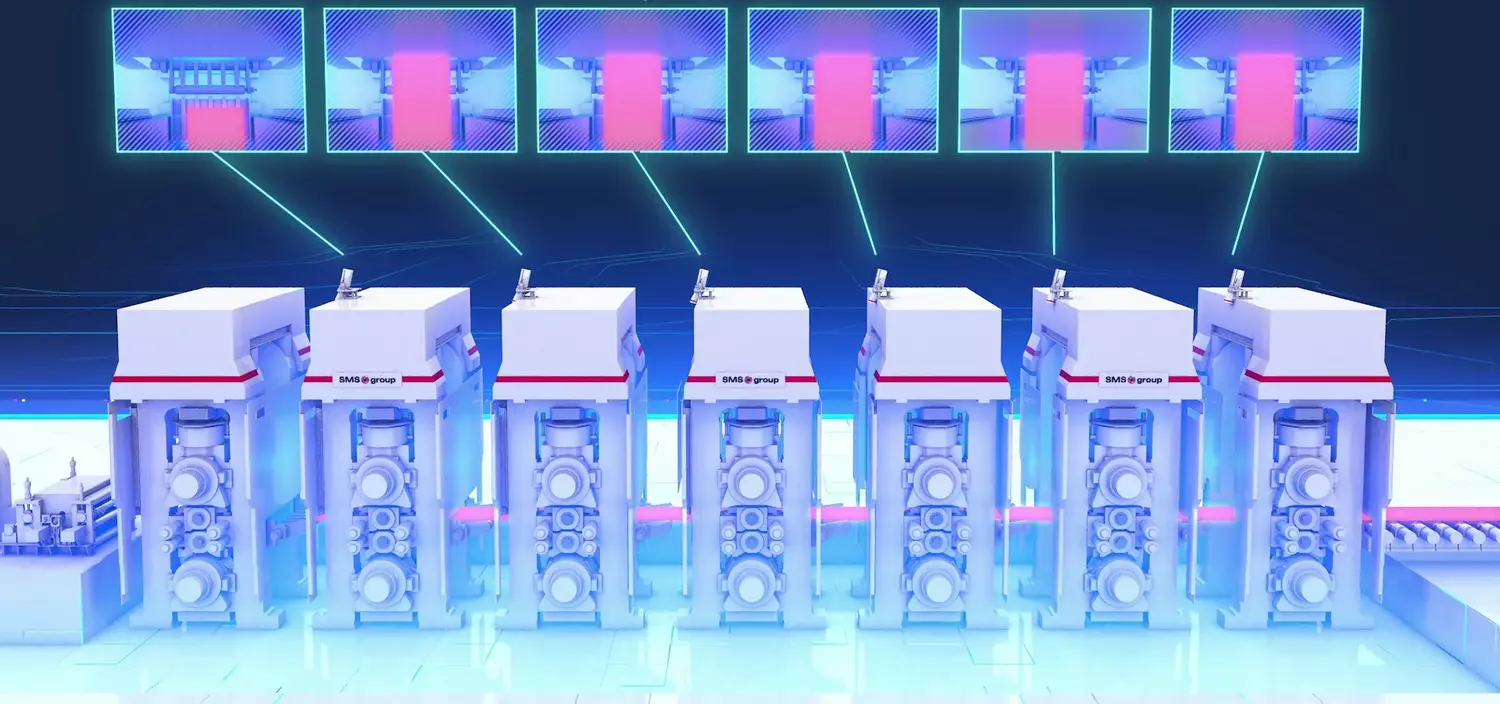
For strip center measurement, the system uses X-Pact® Sense hotCAM designed against harsh environmental conditions like high strip temperature, fog, steam, dust and vibrations. X-Pact® Centerline Control uses a closed-loop algorithm to calculate the strip center line deviation and provides a levelling correction signal for the mill stands. Smooth transition between the control actions in the different phases is ensured.
The control is divided into 3 phases with different control concepts:
- Head: During threading, it can happen that the strip drifts either to the operator side or to the drive side. The camera detects this at an early stage and counteracts it by swiveling the stand. In this case the previous stand is controlled.
- Filet: During rolling the filet it can occur that the entire strip runs to one side or the other. In that case, all stands will be swiveled at the same time.
- Tailend: When unthreading, it is similar to threading, except that in this case the next stand is swiveled.
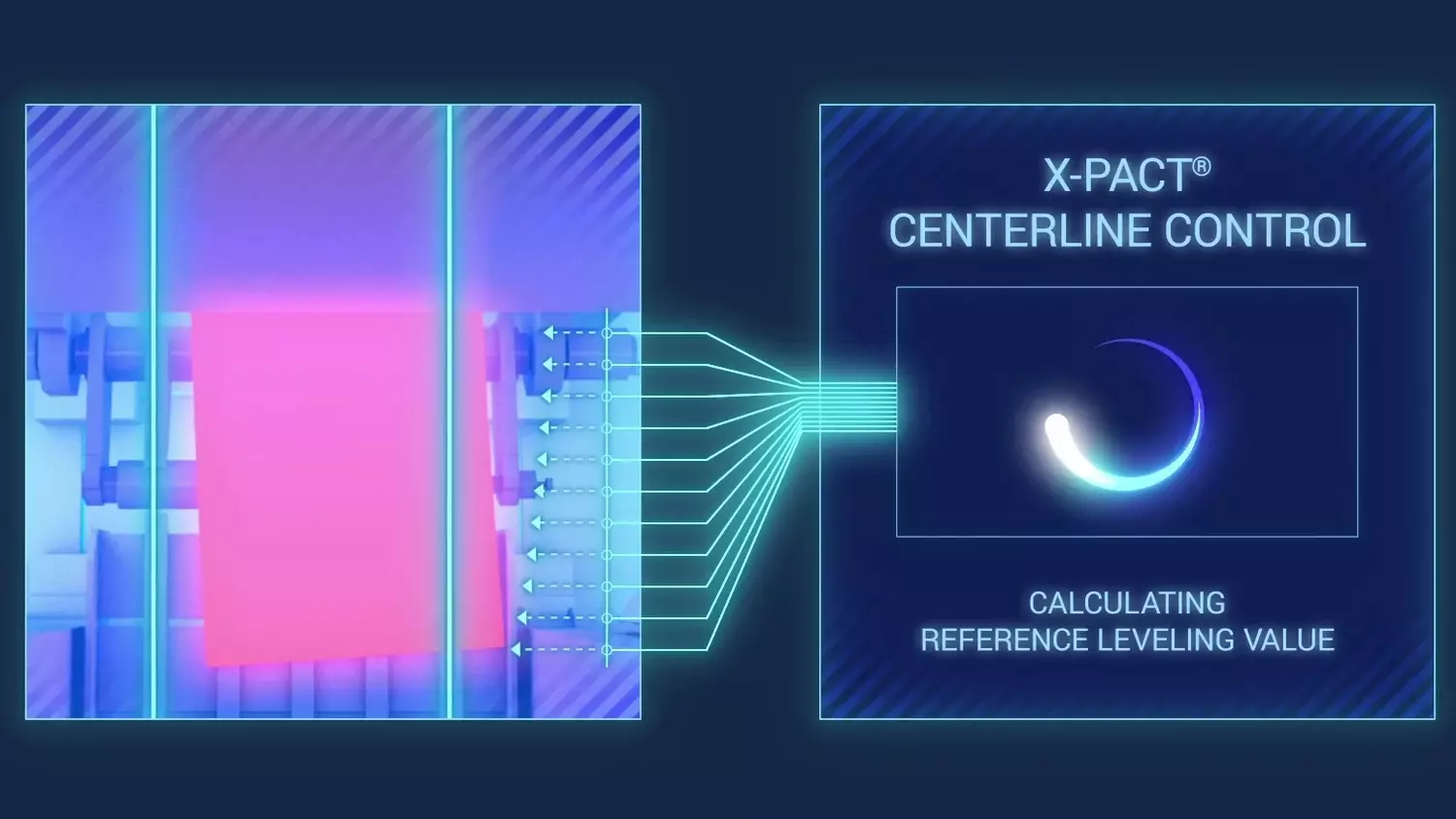
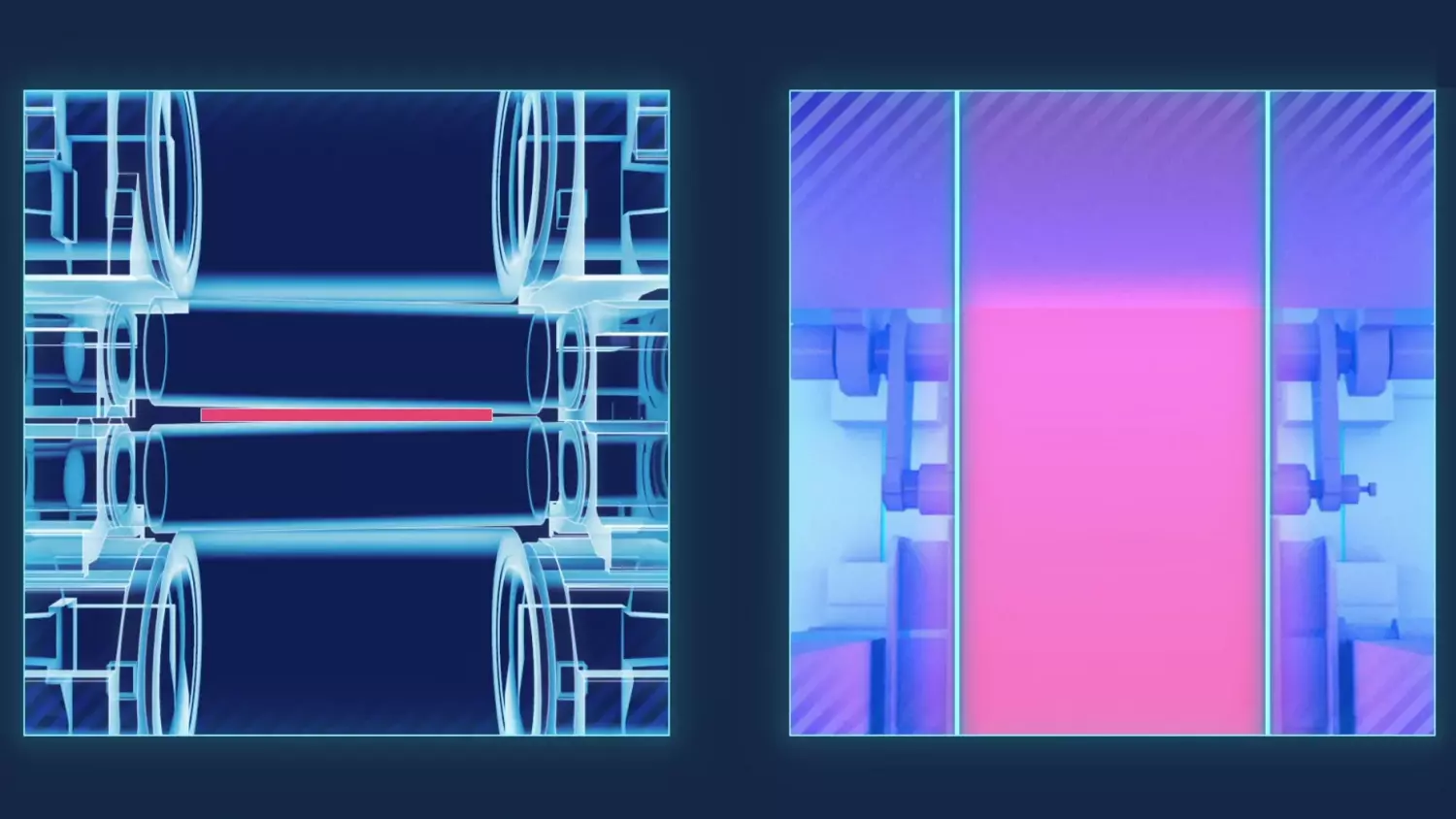
Customer challenges addressed
- Straight and safe strip guidance through the finishing mill, especially for head and tail
- Determination of various measurement values of hot strip material in the hot finishing mill
- Calculation of center line deviation and providing a levelling correction signal for the mill stands