OCTG full-liner for optimized manufacturing processes
For Jochen Schmitz, Head of Product Management Long Products, the new machine is also a strategically important step into the future: “We are pleased to offer our customers worldwide all the technologies for OCTG products with our RMG pipe coupling threading machines, TCG threading machines, and ThreadView measuring systems. Specifically, this is an integrated solution where everything is optimally and harmoniously coordinated.” Jochen Schmitz explains that SMS is responsible for the entire project planning for the integrated facility for automated coupling production: from separating the pipe coupling from the mother tube to optional outside turning, NDTs for crack detection, as well as marking, phosphatizing, painting and packing of the coupling. All process steps are recorded with a seamless tracking system for traceable quality documentation for the premium couplings.
Customized RMG machine concepts
The coupling threading machines are available in the 22, 30 and 38 variants – i.e. with a spindle diameter of 220, 300 and 380 millimeters. The concept of the horizontal coupling threading machine with a turret head and rotary indexing chuck is the perfect solution for premium coupling production, because it combines all value-adding factors including maximum productivity, precision and flexibility. “Our integrated plants, lines, and core machines produce high-quality premium threads at optimal productivity levels, enabling our customers to attain the best competitive position in the market,” says Benjamin Henkel, Sales Manager Cold Finishing Long Products at SMS group.
Our integrated plants, lines, and core machines produce high-quality premium threads at optimal productivity levels, enabling our customers to attain the best competitive position in the market.
Tried-and-true machine rigidity and innovative technologies
The new RMG coupling threading machine is based on the proven, well-established TCG thread-cutting machine. From this machine for premium external and internal threads, RMG gets its core components for a rigid and robust machine tool. “The crucial aspects that ensure high precision and quality are machine rigidity and vibration damping,” says Tim Küppers, Head of Design Department Finishing Lines Cold Finishing, SMS group. This proven basic concept behind the TCG thread-cutting machine also applies to the design philosophy behind the RMG coupling threading machine. What’s more, the low-vibration design of the machine allows the tools to be used for a longer period of time, which has a positive influence on cost-efficiency: That is because low tool wear means fewer shutdown times and minimal operating costs.
The crucial aspects that ensure high precision and quality are machine rigidity and vibration damping.
Efficient and flexible machining processes
The pipe coupling is secured in the rotary indexing chuck. First, the first thread is cut, then the rotary chuck is turned 180 degrees and the second thread is inserted. All machining situations in one set-up offer a huge advantage as regards the centered guidance of both thread sides in relation to each other: The resulting lack of offset is an important feature of the machine’s quality output.
The RMG has six tool holder positions that can be fitted with combination tools. Thanks to the intelligent use of three cutting inserts on the combination tools, three work steps can be performed without having to swivel the tool back in, thereby reducing process times to a minimum.
New gear unit concept for press and pull machining
Another standout feature is the innovative gear unit concept. This allows couplings to be manufactured in both a press and pull machining process. With small-diameter couplings, the press-machining method, where the chips are conveyed inside the sleeve, can be problematic. This is where pull-machining has a decisive advantage: The tool moves into the coupling and, starting from inside the coupling, cuts the thread towards the coupling flat face. This means that a large proportion of the chips is taken out in the process. To allow this machining direction duality, both the RMG coupling threading machine and the TCG pipe threading machine are suitably designed and configured. The workpiece is kept stable throughout the entire process, which guarantees precise and reliable push and pull machining.
Moreover, the chip discharge channel helps to ensure the effective removal of the chips. Here, innovative equipment units such as the high-pressure flushing system, which is directly actuated by the spindle, are used. This solution ensures the effective removal of chips and contributes to optimal process reliability.
Simulate precisely first, then create flawless products
Another innovative feature is the redesigned NC control system in the simplified G code style. It allows quick adjustments of the machine with regard to chip distribution and machining speeds. At the same time, the new coupling threading machine offers a pioneering simulation mode on the generously dimensioned HMI. As a result, changes can be displayed on the monitor before machining commences, and the operator can check whether the programming meets all the relevant requirements and target values.
Well-planned accessibility and serviceability
An important factor in terms of user acceptance is the accessibility of the machine and its individual equipment units for inspection, maintenance, or adjustment work. That is why the engineers at SMS group designed the working area as an open construction. This makes changing the tools much easier. The L-shaped door, which opens upwards, allows unhindered access. Naturally, the RMG comes with all the relevant occupational safety equipment. This also includes the exhaust system, which reliably removes all fumes from the working chamber before it is opened.
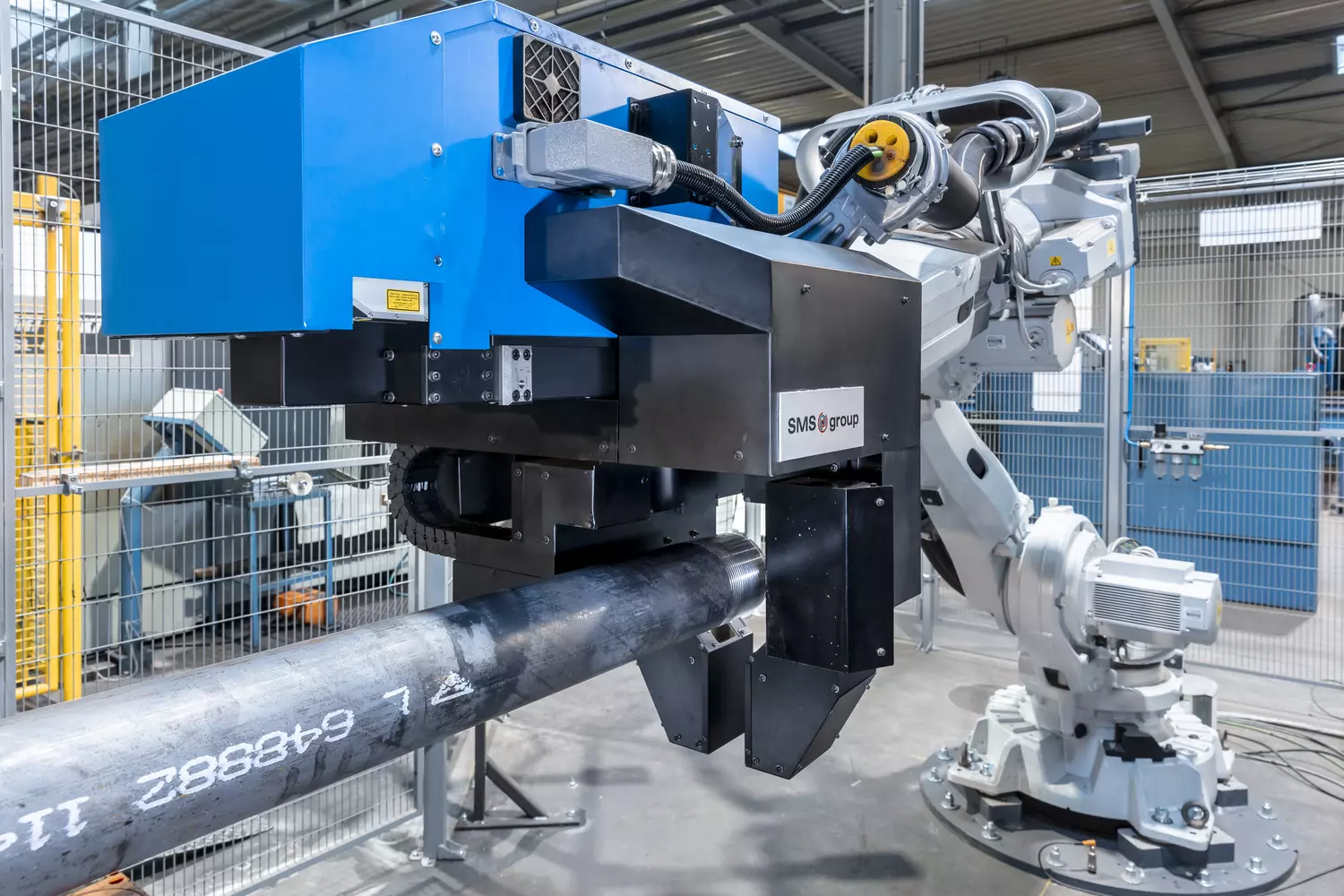
Autonomous quality assurance: ThreadView
The ThreadView measuring system is a groundbreaking innovation in the field of pipe thread quality assurance – particularly when it comes to producing flawless premium OCTG pipes. ThreadView enables the autonomous measurement, assessment and documentation of all cut threads, thus ensuring seamless quality control. Any deviations are detected as soon as they occur.
Capable of being integrated directly into the thread cutting line, the system will in future allow the completed threads to be fully measured, which significantly increases production output. ThreadView not only assists with the measurement of threads with a negative flank, but also enables the creation of individual, detailed test reports for each individual thread, ensuring precise traceability.
Automating the inspection process reduces the need for personnel and minimizes material losses as defects are detected early on. Overall, the ThreadView system is thus a highly efficient solution for testing threads. It makes a significant contribution to increasing production, reducing costs, and ensuring lasting quality assurance.
Conclusion
With the introduction of the RMG coupling threading machine, SMS group is positioning itself as a full-liner in OCTG production. The new machine with its unique technological innovations completes SMS group’s comprehensive portfolio of solutions for manufacturing OCTG products. Thanks to its efficiency, quality, flexibility, and economy, the RMG is a welcome addition to our product portfolio and offers customers all over the world a seamless, high-quality production chain – from precise machining to seamless quality control. In this way, SMS is defining new standards as a holistic supplier in the field of OCTG manufacturing technology and strengthening its position as market leader.
Contact: Benjamin Henkel