Reducing the global carbon footprint in increasingly complex and volatile markets requires new ways of thinking, a willingness to change, and the use of disruptive technologies. SMS already offers not only new processes and equipment for the production of high-performance materials in the field of metallurgy but also digitalized and connected processes as part of Industry 4.0 aimed at realizing the fully autonomous steel plant. In the following, we will look at three use case examples of the DataXpert platform and outline the opportunities this presents for predictive asset optimization and why the interaction of different disciplines is essential for developing modern digital solutions.
Digital applications provide the leverage for resource-efficient and sustainable production processes, which are now playing an increasingly important role in the manufacturing industry. They enable plant operators to make accurate, machine learning-based predictions about production processes, product quality, and the plant’s condition. Similarly, energy consumption can be predicted and optimized through the targeted calculation of raw materials. The possibility of making accurate process predictions means that raw materials and feedstock are used according to demand, thus reducing waste, downtime, and costs. By relying on digitalization, companies can generate enormous added value from the possibilities offered by new technologies such as machine learning for the holistic optimization of production processes.
Another important topic, however, is occupational safety, and machine learning methods provide an opportunity to make important further developments. Today, for example, camera systems allow problems to be detected without humans having to enter hazardous areas. New sensor technology helps to assess the state of the production line with ever-greater precision. Condition and process monitoring systems combine data from multiple sources to provide plant operators with meaningful information and recommendations. Predictive asset management and automation will be instrumental in improving safety and mitigating risks in steel production facilities. Digital tools enable us to anticipate, respond to, and solve problems before they occur. The aim is to create next-generation steel plants that operate fully autonomously, efficiently, and safely.
SMS group developed the DataXpert platform to facilitate the collaboration between interdisciplinary teams of software developers, experts with process and hardware knowledge, and data engineers and data scientists. So, what are the specific possibilities for using platforms for efficient plant management?
Utilizing digital solutions for more sustainable and efficient steel production
DataXpert is designed as a complete platform for developing and managing condition monitoring and expert systems that provide real-time recommendations and notifications. The platform uses the low-code principle, which allows users with little or no programming knowledge to use the tools with little training. DataXpert consists of three main modules, BIXpert, AIXpert and RulesXpert, and is coupled with a powerful time series database. Each platform tool is modular and can be extended to include additional functions via plugins, e.g., new data connectors, new visualization types, modules with new function blocks, etc. Thanks to the use of web technologies, the platform can be deployed in the cloud and on a server close to the plant.
The DataXpert platform and its components is shown in Figure 1. The platform provides software solutions for:
- Data acquisition, storage, description, validation, and replication (data lake).
- Logic/model generation and testing (RulesXpert Designer, AIXpert)
- Logic/model execution (RulesXpert Scheduler)
- Data visualization (BIXpert)
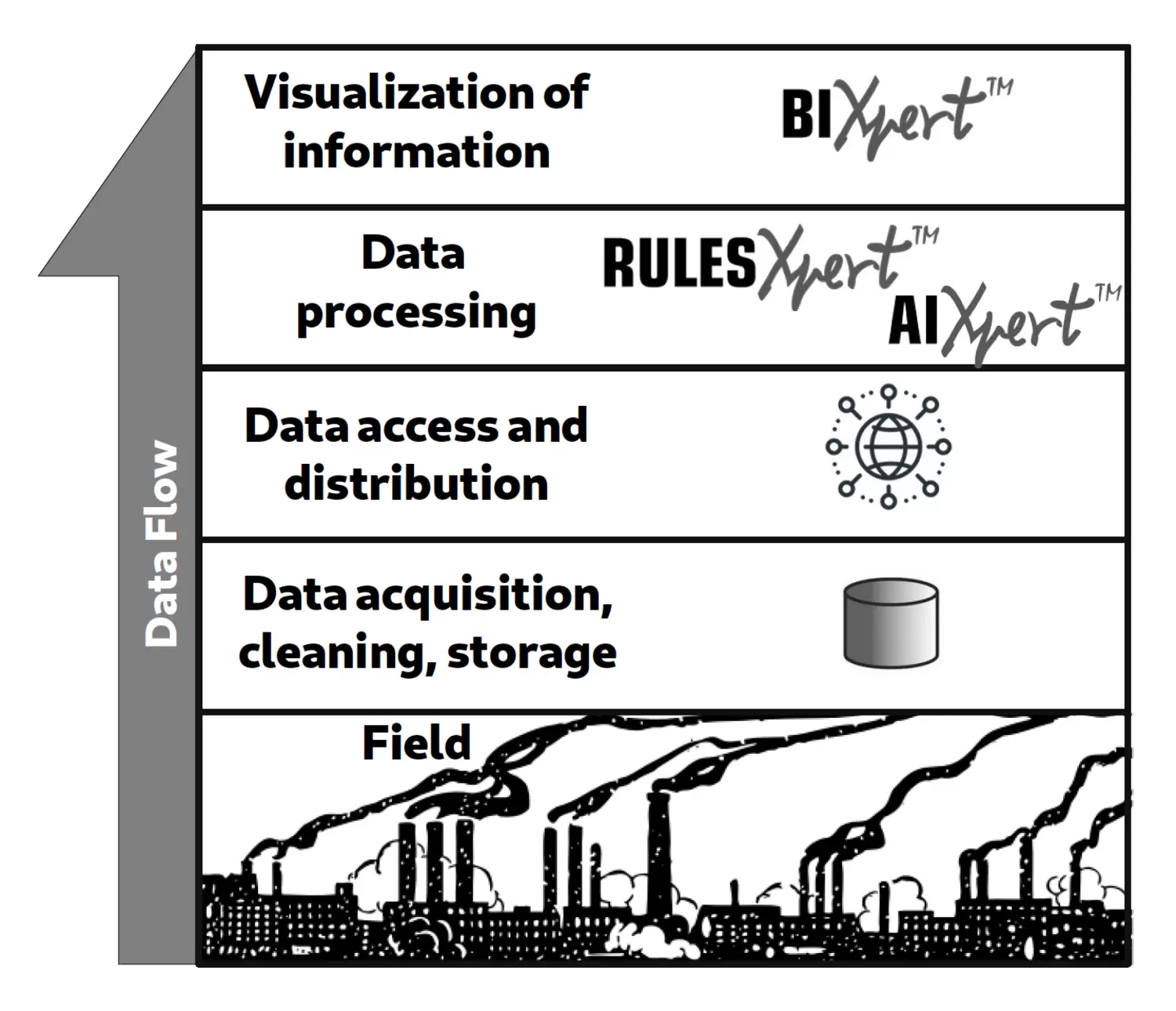
Application examples for condition monitoring
The integration and utilization of machine learning models in the DataXpert platform is further illustrated with use case examples. The platform is an integral part of the Smart Maintenance program at Paul Wurth, from which the following examples are taken, and became the Asset Optimization Platform at SMS digital for steelmaking processes. DataXpert is already being used to combine various machine learning models in different programming languages or to tag time series data and then invoke a model based on that data in a low-code environment.
Pattern recognition for discharging the Bell Less Top
The first example is a model written in Julia for detecting charging patterns in BLTXpert. BLTXpert is a condition monitoring solution for the Bell Less Top that provides alerts and notifications on a range of phenomena or anomalies as well as recommendations for equipment maintenance and operation. SMS has deployed a machine learning model as part of the rules that cross-check signals received from the stock house. The model is executed for every discharge of the Bell Less Top. A pattern detection algorithm, based on a convolutional neural network and trained with the Flux library, analyzes the motor signals from the rotary and tilt motors to distinguish between material types.
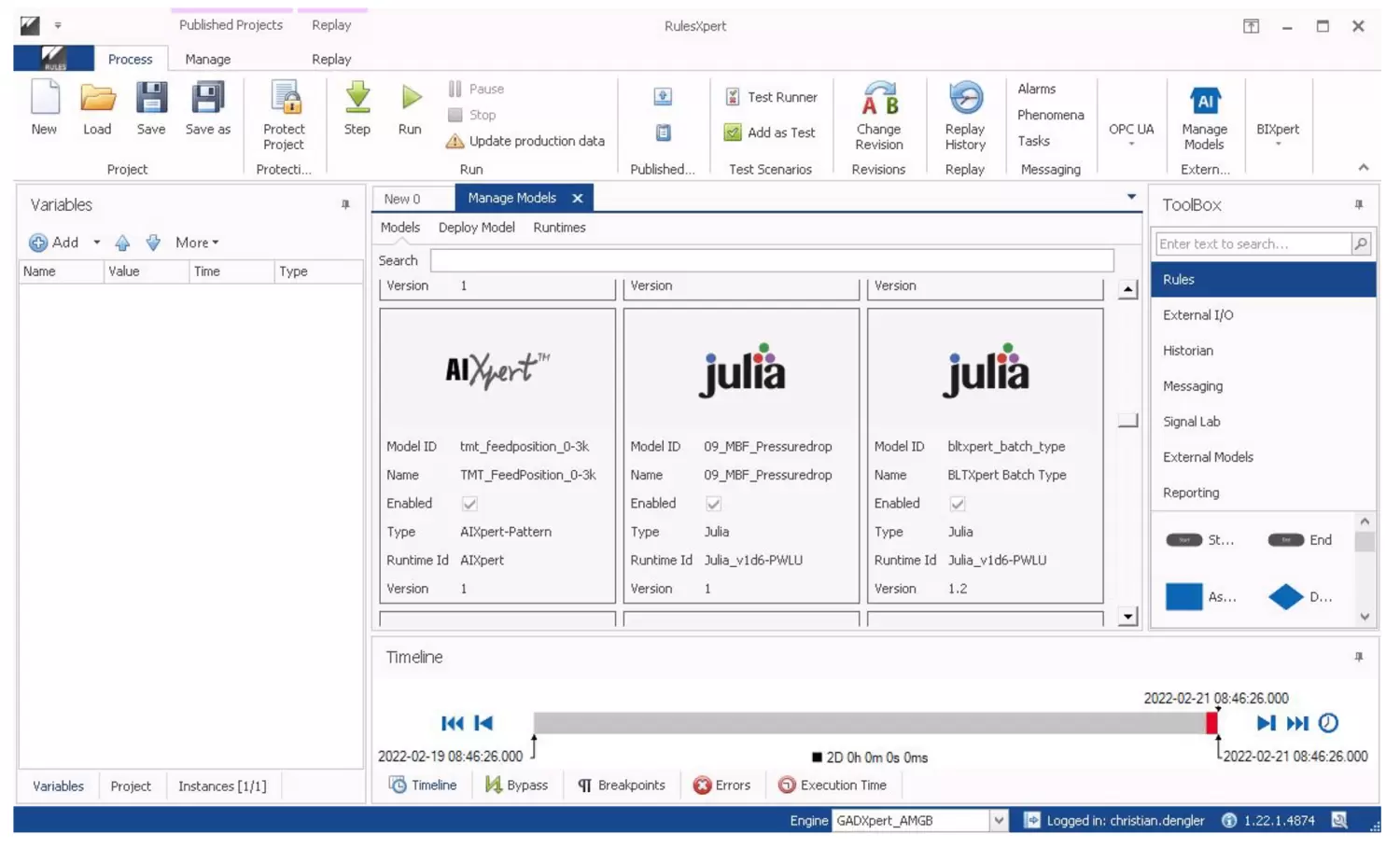
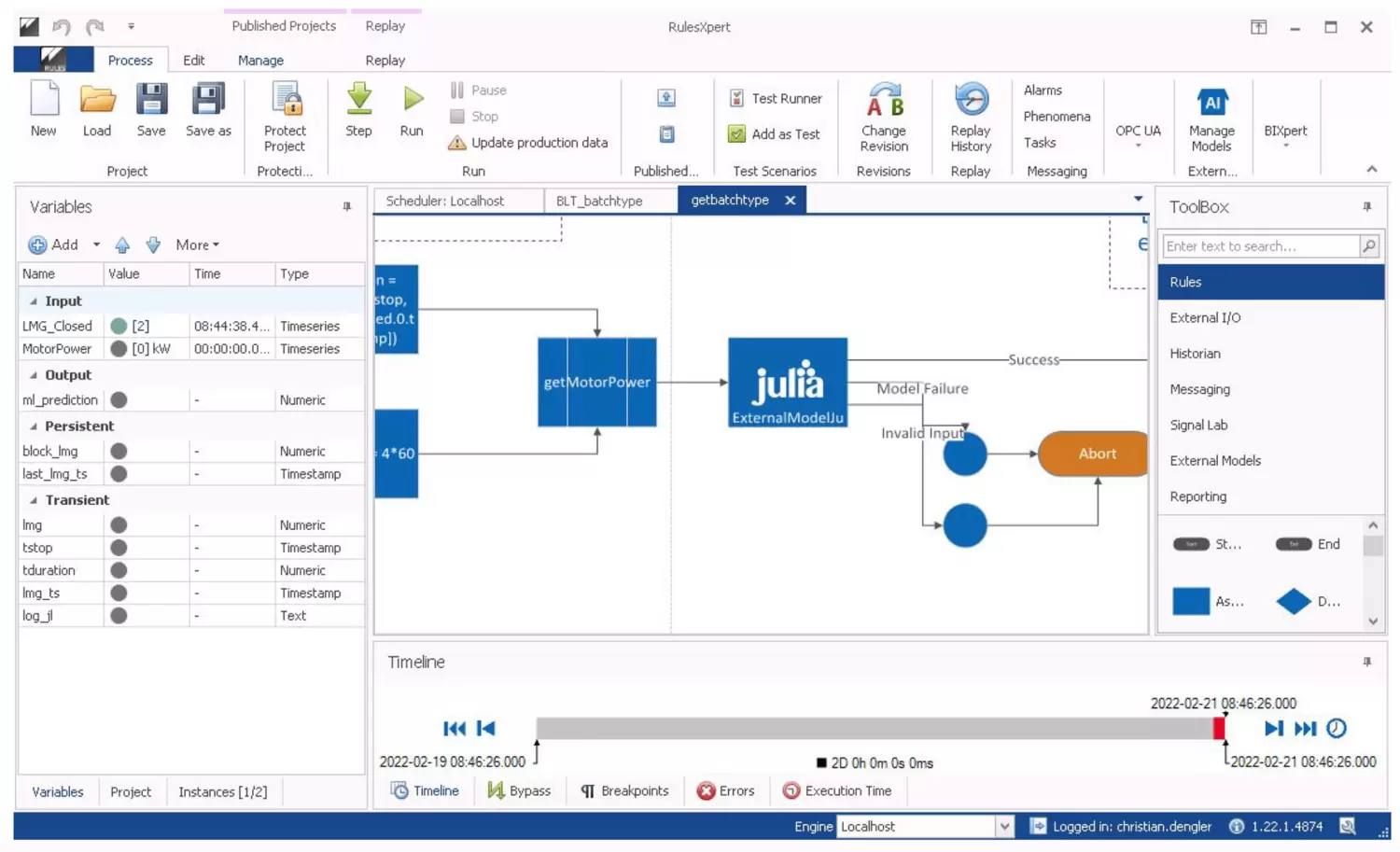
Notifications for potentially incorrect material information and a dedicated dashboard for the justification of the machine learning output is provided in BIXpert by clicking on the triggered notification. This justification dashboard, taken from a BLTXpert demo, is shown in Figure 3. A data scientist is responsible for developing, integrating, and maintaining the machine learning model. An equipment expert defines and implements the rules and notifications for this use case, resulting in a clear separation of responsibilities and efficient application of the skills available in each department.
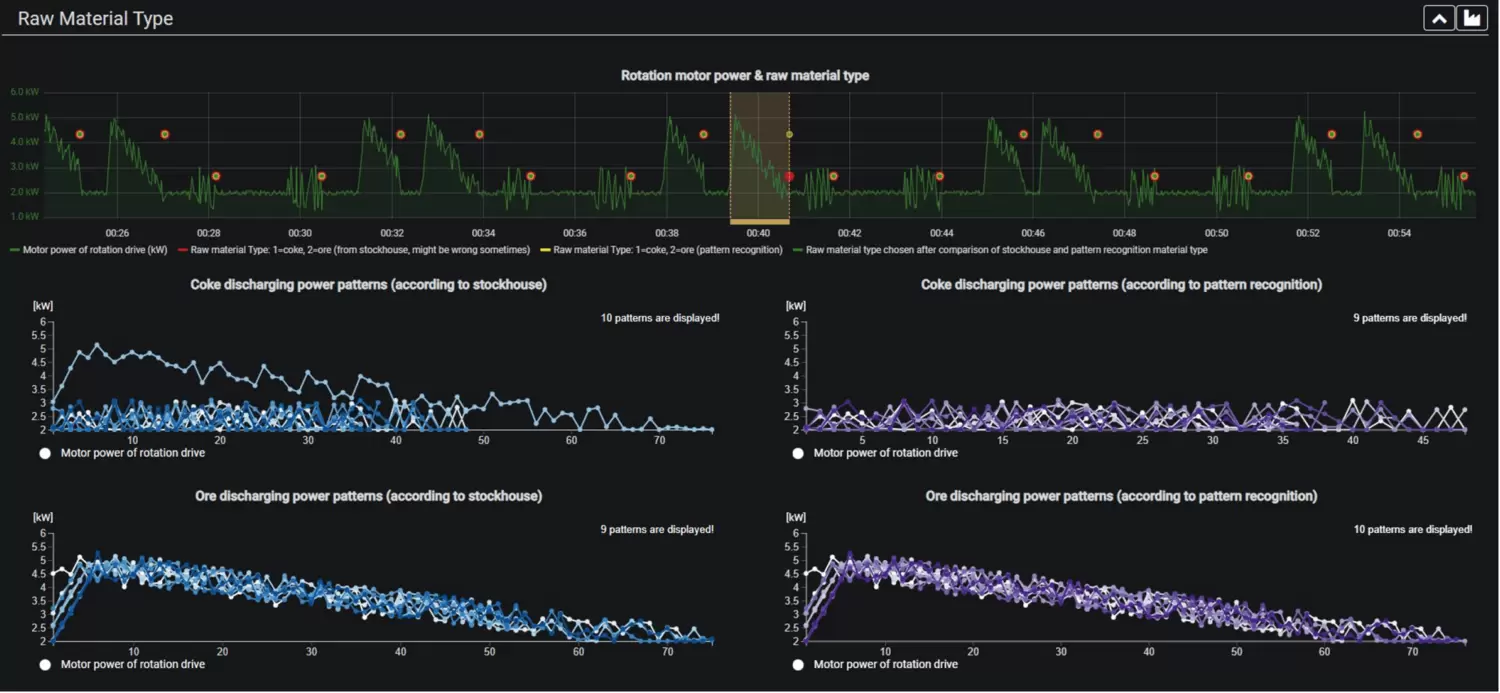
Opening detection for tapping machines
Paul Wurth worked in collaboration with TMT to develop a process and condition monitoring system for cast house machines called Tapman. One process rule of Tapman deals with the classification of tapping operations and the distinction between "pre-drilling" and "opening." To detect an opening of the taphole immediately after drilling, a machine learning model analyzes the shape of various signals, mainly the feed position, to classify the taphole. In the case of a misclassification, the signal is subsequently corrected when the taphole is closed. The model in this case is a convolutional neural network written in Python using the Tensorflow library. The model is being developed by data scientists at Paul Wurth, while TMT defines and implements the rules of Tapman. In this case, DataXpert is used not only to separate the work activities and responsibilities but also for data labeling. Process experts from TMT labeled the data in BIXpert to provide training targets for the data scientists. The output of this model is an input to several other rules, such as a rule that determines the taphole depth and the recommended clay mass to close the taphole.
Hot metal temperature prediction
The third example of a machine learning application is taken from ProcessXpert. ProcessXpert is part of BFXpert and provides process information and recommendations for actions for the blast furnace process. As an optional add-on to ProcessXpert, a machine learning model can predict the temperature of the hot iron up to three hours in advance. This information can be used to adjust the process in case of undesired temperature profiles. A model ensemble approach is used to predict the hot metal temperature. As described previously, the models that are part of the ensemble are deployed, invoked, and combined in RulesXpert. Some of the models are written in the R language using libraries such as xgboost and randomForest, while some models are trained in AIXpert. Here, DataXpert facilitates the deployment and use of the model by combining and managing the execution of all models.
How does machine learning contribute to this?
Machine learning enables us to draw better conclusions in data-rich decision areas and helps us to assess equipment health and detect complex anomalies from real-time sensor data. Thanks to machine learning, equipment failures can be predicted or, at the very least, a probability of failure assessed days in advance. It uncovers characteristics and sensor-level factors that cause a failure. Finally, it reduces huge volumes of data down to a specific amount of relevant information. Ultimately, data-driven condition monitoring does the groundwork for the learning steel plant. By providing real-time insights into the plant’s condition and process deficiencies as well as predicting machine failures, maintenance measures can be taken proactively and production can be rescheduled and productivity increased.
Conclusion
The tools in the DataXpert platform facilitate the development and deployment of machine learning models. The workflow in DataXpert enables the separation of responsibilities and the invocation of machine learning models from a low-code environment. In the future, RulesXpert will be available as a web application to provide even easier access for people from different backgrounds to integrate their knowledge and models in one central location. In addition, an option for Git, a popular system for code version control, will be integrated into ModelManager to allow models to be updated remotely in an automated manner.
High plant availability and maximum product quality are key performance indicators in the operation of a plant. Artificial intelligence and machine learning have made great strides in recent years and are being used in industrial manufacturing to achieve these goals. When plant know-how, process modeling experience, and modern data science are intelligently combined, the profitability of a steel mill can be significantly increased.