With the Scrap Management Suite, SMS has developed a tool for reducing a company's carbon footprint while cutting production costs at the same time. The main functionality of this well-established scrap management system is to collect process and material-related information on the scrap yard. This mature tool now also comes with innovative artificial intelligence methods and mathematical models to evaluate the tracked information in such a way that the overall efficiency per ton of scrap used is enhanced significantly.
Compared with other metal-making processes, such as primary or secondary metallurgy, the use of recycled materials is subject to manual processes that are not as highly automated. Generally, the IT production system does not capture sufficient information on the handling and composition of the scrap. This means that the important data required for production are not available in digital form. The uncertainty associated with this poses considerable challenges with regard to both production planning and control.
Tracking of scrap handling
The charging of the scrap container and thus the crane operator play an important part in the scrap handling process: scrap containers must be filled with the specified recipes for the charge materials in the correct order and weight within the shortest possible time. SMS's Scrap Yard Management system provides assistance here by recording the key events in the crane's movements. This allows scrap handling within the scrap yard to be tracked and the set recipes to be compared in real time with the scrap that is actually charged. The crane driver can use an operator panel in the crane to check the loads he has already carried out any time he chooses and, if necessary, adapt the scheduled loading process. For outdoor scrap yards, there is also the possibility of tracking all vehicles and any completed process steps via an app and instructing and guiding the operators in order to ensure complete transparency in outdoor working areas too.
The detailed recording of all sequences significantly improves stock level documentation. What's more, the scrap heap volume can be captured by means of laser scanners on the crane beam and a precise volume model can be created to calculate the exact stock level down to just a few kilograms. This allows orders to be placed more precisely and any ordered materials no longer have to be stored for an indefinite period at considerable cost. Here SMS collaborates with the experienced laser-based application provider LASE Industrielle Lasertechnik. Short storage times also reduce the oxidation of the material, which in turn increases yield and reduces CO2 emissions. The laser scanner also provides a precise calculation of the fill level of the scrap container - down to a few centimeters - and thus ensures optimal filling of the container. Using a laser scanner for material detection is the first important step towards autonomous crane operation.
The material handling process in the scrap yard is also visually documented. Cameras record the scrap unloading process. Each incoming scrap load is also allocated to the wagons and trucks as they arrive, so that the origin of every scrap delivery can be determined and the scrap quality from any given supplier fully validated. This is where SMS goes a step further and uses artificial intelligence to classify the scrap types during the unloading process. Image recognition algorithms simplify a large number of activities that currently need to be performed manually and are very time-consuming. Furthermore, all scrap container charging processes are visually documented, so that the relevant process can be examined and optimized, if necessary, with regard to the target analysis.
The material handling process in the scrap yard is also visually documented. Cameras record the scrap unloading process. Each incoming scrap load is also allocated to the wagons and trucks as they arrive, so that the origin of every scrap delivery can be determined and the scrap quality from any given supplier fully validated. This is where SMS digital goes a step further and uses artificial intelligence to classify the scrap types during the unloading process. Image recognition algorithms simplify a large number of activities that currently need to be performed manually and are very time-consuming. Furthermore, all scrap container charging processes are visually documented, so that the relevant process can be examined and optimized, if necessary, with regard to the target analysis.
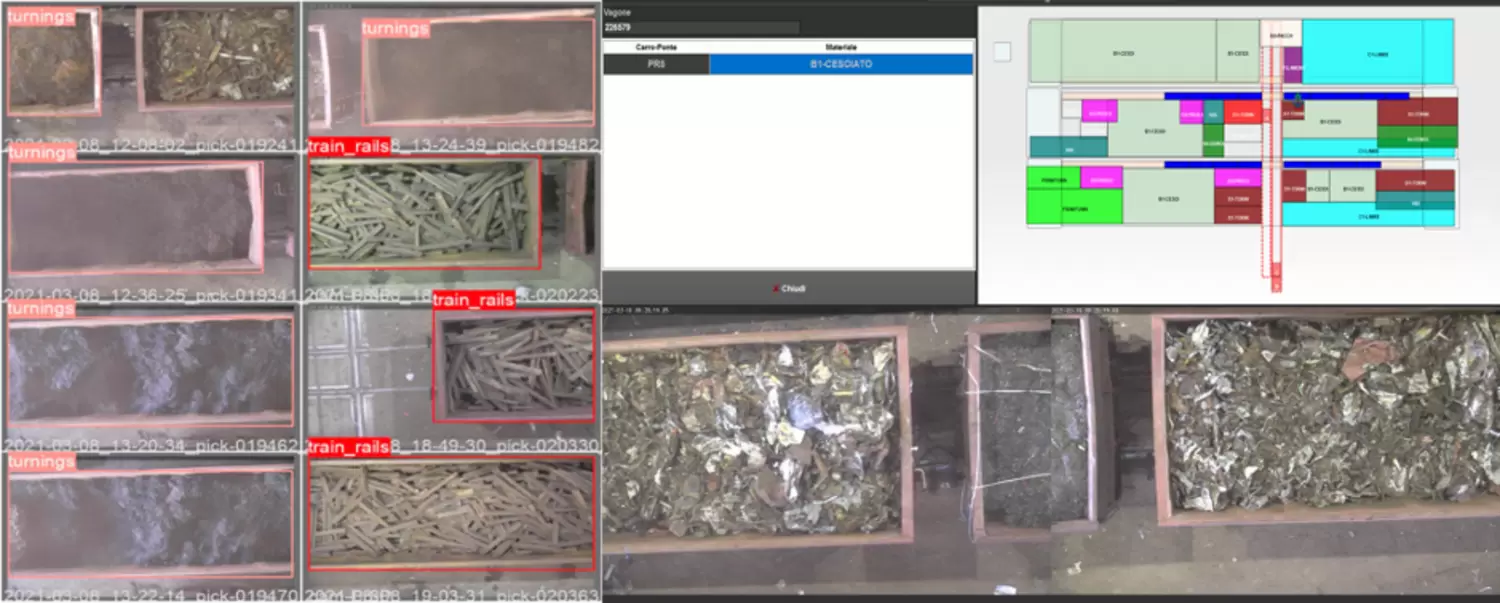
Scrap characterization
At present, optimization algorithms aimed at cutting costs for charging raw materials are only rarely employed in the global steel industry. Instead, standard operating procedures (SOPs) are followed. In order to minimize the risk of not achieving the target analysis, high-quality scrap and products from direct reduction are predominantly used for charging. Severe fluctuations in the chemical composition of individual batches can be compensated in this way, but they result in safety margins that do not take account of considerable savings potential. Currently, optimization algorithms are barely used at all – there is too much uncertainty regarding the chemical composition of the scrap.
SMS designed and built AI applications specifically to address this problem. Using historical chemical analyses of the melt, these machine-learning models are able to make predictions on the chemical composition of those scrap types currently stored in the scrap yard. The prediction of the chemical composition of the scrap type is used for an optimization algorithm that calculates the most cost-effective scrap mix for the target analysis and reduces the proportion of direct reduced iron to a minimum. In addition to cutting raw material costs, the reduction in CO2 emissions is a further positive side effect.
SMS designed and built AI applications specifically to address this problem. Using historical chemical analyses of the melt, these machine-learning models are able to make predictions on the chemical composition of those scrap types currently stored in the scrap yard. The prediction of the chemical composition of the scrap type is used for an optimization algorithm that calculates the most cost-effective scrap mix for the target analysis and reduces the proportion of direct reduced ironto a minimum. In addition to cutting raw material costs, the reduction in CO2 emissions is a further positive side effect.
In the past, scrap yard management often played only a minor role in the manufacture of metal products. Due to the growing cost pressure faced by the manufacturers and the shift towards more sustainable production processes, scrap yard management is increasingly becoming a significant distinguishing feature that makes a company stand out from its competitors. By extending the Scrap Management Suite with digital modules, SMS is taking a major step in this direction. In particular, the interaction between scrap handling tracking and scrap characterization increases the recycling rate while at the same time ensuring more efficient use of the material. Just a few measures are enough, therefore, to reduce CO2 emissions significantly. In no other stage of the value chain in an existing plant can such a positive effect on the CO2 balance be achieved at reasonable cost.