Flexible concepts for aluminum strip and plate
You are guaranteed to benefit from our long-standing technological expertise in hot rolling processes for the aluminum industry. It is not for nothing that we are the global market leader for aluminum hot rolling mills for both plate and hot strip production. We supply the full range of equipment and services from one source.
Nexcast – The next generation minimill
Casting and rolling of aluminium strips in one continuous production process. The new Nexcast minimill produces strips of all kinds of aluminum and aluminum alloys, with sufficient surface quality for most applications, good to very good thickness-, profile- and flatness tolerances and very stable final rolling temperature over the strip body length.
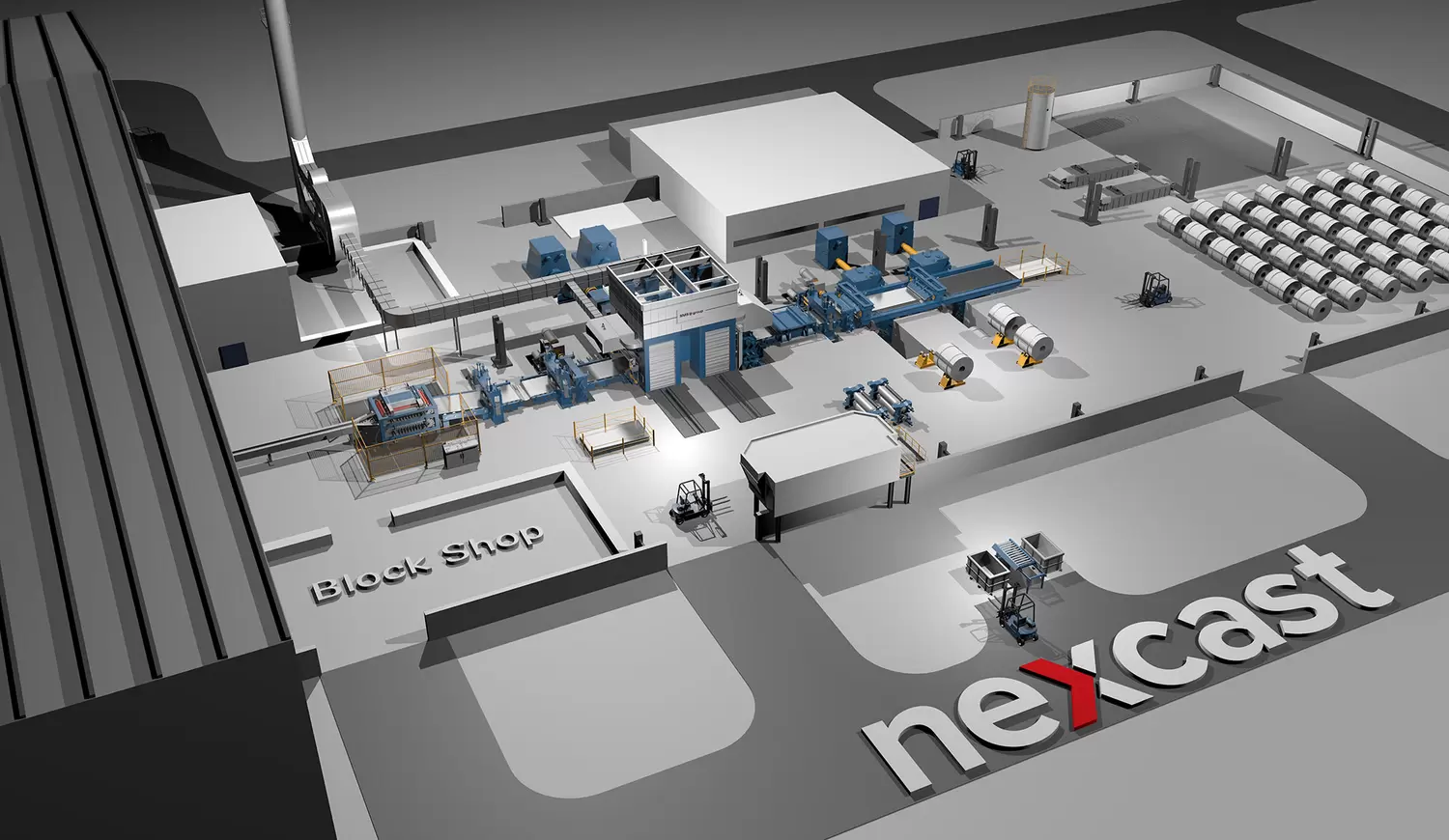
-
Reversing plate mill
Plates of all kinds of aluminum and aluminum alloys
Main dataProduction of aluminum plates with good surface quality, thickness tolerance and profile.
Layout of Reversing plate mill for aluminum -
Compact single-stand reversing mills
One mill for aluminium plates and strips
Main dataThe application for this most compactly designed plant is the production of strips and plates of all kinds of aluminum and aluminum alloys with sufficient surface quality, thickness-, profile- and flatness tolerances as well as final rolling temperature over the strip body length.
Layout of single-stand reversing mill for aluminum -
Reversing mills for strip (1 + 1)
Compact but capable for aluminum strips and plate
Main dataRolling of strips and plates of all kinds of aluminum and aluminum alloys, with good surface quality, good to very good thickness-, profile and flatness tolerances and good final rolling temperature over the strip body length.
Layout of Reversing mill for aluminum strip -
Semi-continuous hot mill lines for strip and plate (1 + 4)
High production capacity - excellent product quality
Main dataOn the 1+4 hot rolling line strips of all kinds of aluminum and aluminum alloys with best surface quality, excellent thickness profile and flatness tolerances and perfect final rolling temperature.
Layout of semi-continuous aluminum mill
SMS group email service
Our promise to you: this is not just another newsletter!
Use our contact form for questions, inquiries or personal contact.
-
Ingot scalpers for main ingot surfaces and ingot edges
Excellent surface quality for hot rolling
The ingot scalpers are installed upstream of the hot rolling mill. They remove the oxide skin as well as any metallurgical impurities from the surface of the ingots. Scalping the edges reduces the amount of trimming scrap generated in the subsequent hot rolling process and keeps the work rolls clean. Another impressive feature of our ingot scalping machines is their high rigidity. That guarantees the best surface qualities right down to micron level – even on hard aluminum alloys.
Designs:
- Single-head ingot scalping machines with turntable for machining ingots in horizontal position
- Combined edge and surface scalping devices for simultaneous horizontal scalping of main surfaces and edges
- Two side-mounted milling heads for machining ingots in vertical position
-
Edging stands
Higher yield, flexible design
You want to increase yield by reducing trimming losses. Our edging stands are perfect for this job. That’s because each edging pass enhances the strip edge quality. This cuts trimming losses.
Our edging stands are designed for flexible integration into roughing mills. Stand-alone edgers are ideal for plate mill stands where it’s important to turn the slab for cross rolling and precise slab centering/guiding. Equally ideal for strip production lines, the edger is directly attached to the roughing stand to reduce reversing times and increase yield. Depending on your requirements, we install the edger gears above or below the pass line.
4-hi roughing stand -
Transfer bar cooling
Cooling boosts production
Our transfer bar cooling system allows the yield to be considerably increased. Installed in the entry section of the finishing mill, the system precisely sets the final strip rolling temperature, so you benefit from shorter holding times and higher yield.
Entry of finishing mill -
Mill stand actuators
Close plate and strip tolerances
Our mill stands come equipped with powerful actuators so you can produce hot strip and plate to close thickness and profile tolerances. Specifically, these actuators are:
- Mechanical and hydraulic gap adjustment systems
- Work roll bending
- CVC®plus
- Multizone cooling
CVC® plus is the world’s most successful technology package for profile and flatness control. It combines axial work roll shifting with special CVC® grinding, a work roll bending system, and our powerful technological process model (Profile and Flatness Control, PFC). This PFC uses – for each strip – the pre-calculated values for roll force in terms of roll temperature and roll flattening to calculate the optimum pre-settings for the work roll CVC® shifting position and bending force. Then it automatically adjusts the roll gap to the changing conditions. The result? Extremely close strip tolerances. Due to the wide setting range provided by CVC® plus, our mill stands typically feature negative work roll bending only. This cuts maintenance compared to stands with both negative and positive bending.
Rolling mill stand -
Work roll brushes
Excellent surface quality
You can rely on our work roll brushes to keep your rolls free from aluminum oxide pick-ups. That ensures excellent strip surface quality and longer-lasting work rolls under the required roughness conditions. The brushes oscillate across the work roll barrel and guarantee uniform cleaning of the roll surface. Due to a special low-vibration design, our work roll brushes achieve an excellent cleaning effect.
-
SIEFLEX®-HT gear-type drive spindle
High capacity spindle
Our SIEFLEX®-HT gear-type spindles are engineered to transmit drive torque to the finishing mill work rolls. Involved here are a new hardening process, an optimized tooth design, and a special tribo-system, which enormously enhance the performance of these shafts. As a result, SIEFLEX®-HT spindles pack up to double the torque of conventional gear-type drive shafts.
To facilitate work roll shifting, SIEFLEX®-HT spindles include longer internal toothings of the sleeves on the mill pinion side. They achieve shifting distances of more than +/- 200 mm and deflection angles of up to 3°.
Equally effective is the continuous oil lubrication system included in SIEFLEX®-HT spindles. It thoroughly cools the spindles during operation. Plus, due to the constant oil flow, there is no need to maintain grease levels and deal with environmentally polluting grease. All this significantly extends spindle service life and reduces mill downtimes.
Sieflex spindle -
SMS giant torque spindles
Higher torques and safe operation
As a result of systematic developments in materials, geometry, and the tribo-system, SMS giant torque spindles can transmit torques up to 40% higher than conventional slipper-type spindles. That means they out-perform even high-end cardan shafts. Moreover, SMS giant torque spindles are safe to operate without expensive safety clutches.
Traditionally, slipper-type spindles are used to transmit the drive torque to the work rolls. It's due to their simple and sturdy design that they easily absorb overloads and shocks in the elastic range. That gives them an extremely long service life.
Services for your plant
Sorry, there are no results for the search term.