Hohe Flexibilität und breites Produktionsspektrum
Ausgangspunkt der neuesten Entwicklung von „SHAPEView“ und „SHAPEControl“ war das Berechnungsmodul „SHAPEBase“, das bereits seit 2013 zur Berechnung der Prozessparameter beim JCO®-Rohrformen eingesetzt wird. Der JCO®-Formprozess zeichnet sich insbesondere durch seine hohe Flexibilität und das entsprechend breite Produktionsspektrum mit Rohrdurchmessern von 16 bis 64 Zoll (406 bis 1.626 Millimeter) mit Wandstärken bis über 45 Millimeter aus. Um die flexibel einstellbaren Parameter der Rohrformpresse optimal auf die jeweilige Produktion abzustimmen, hat SMS für ihre Kunden die Software „SHAPEBase“ entwickelt. Damit ist der Kunde zum einen in der Lage, sich von der Software grundlegende Maschineneinstellungen vorschlagen zu lassen: Hierzu zählen unter anderem der zu verwendende Werkzeugradius, der einzustellende Unterwerkzeugabstand sowie die optimale Anzahl an Biegeschritten. Zum anderen werden auf Grundlage dieser Maschinenparameter zuverlässige Startparameter für den Biegeprozess berechnet und ausgegeben.
Insbesondere werden die Positionen der einzelnen Biegeschritte auf dem Blech sowie die entsprechende Eintauchtiefe des Biegewerkzeugs vorausberechnet. Bei der Berechnung der Eintauchtiefe ist neben der aktuellen Biegekontur vor allem die Rückfederung nach dem Biegen zu beachten, die im Wesentlichen von Wanddicke, Streckgrenze und E-Modul abhängt. Ergebnis der „SHAPEBase“-Berechnung, die offline auf einem beliebigen PC zur Produktionsplanung erfolgen kann, ist somit eine theoretische Rezeptur zur Einformung des gewünschten Rohres. Bei der theoretischen Vorausberechnung können gewisse Einflussgrößen nicht berücksichtigt werden. Hierzu zählen vor allem Schwankungen der Wanddicke und der Streckgrenze des einlaufenden Bleches, das mit mehr oder weniger hohen Toleranzen behaftet sein kann. Entsprechend werden in der Praxis die Prozessdaten – vor allem die Eintauchtiefe des Werkzeugs – von Rohr zu Rohr an die aktuelle Blech-Charge angepasst.
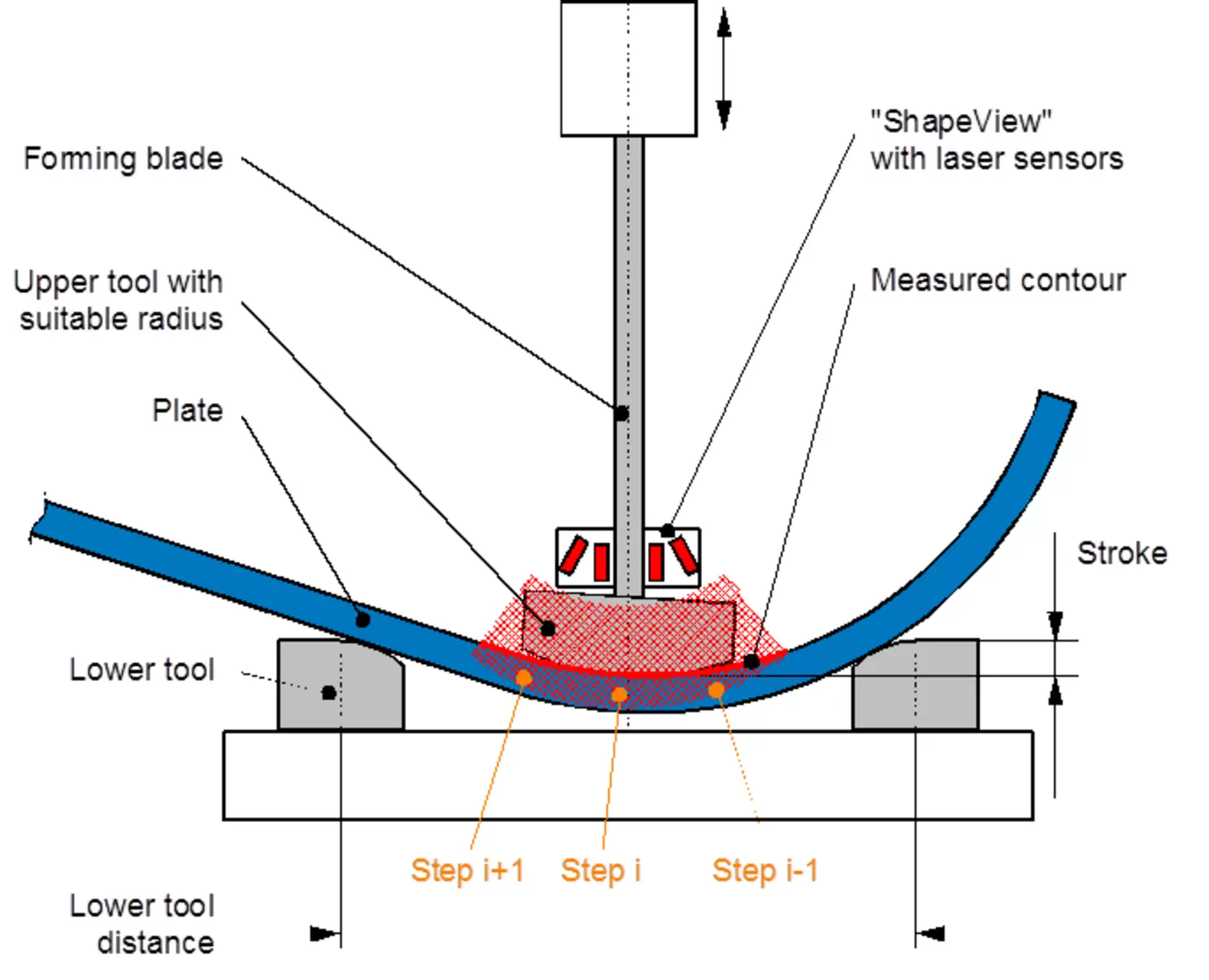
Üblicherweise werden zum Einfahren der Produktion bis heute Radien-Schablonen verwendet, deren Anwendung auch für erfahrene Bediener vergleichsweise zeitaufwendig ist. Treten innerhalb der Blech-Charge jedoch Schwankungen auf, so sind diese schwer zu erkennen und manuell kaum zu kompensieren. Zudem kann es durch kleine Ungenauigkeiten in der Blechpositionierung zu Abweichungen bei der Einformung kommen. An dieser Stelle bietet das neue „SHAPEView“-System eine optimale Ergänzung der theoretischen Berechnungen aus „SHAPEBase“. Nach jedem Formschritt wird die aktuelle Rohrkontur mit Hilfe von Laser-Lichtschnitt-Sensoren in einem definierten Querschnitt detailliert erfasst. Das System stellt aber nicht nur eine digitale Schablone dar, sondern „denkt“ im angekoppelten Modul „SHAPEControl“ einen Schritt weiter. Die gemessene Kontur wird hierbei mit der theoretisch erwarteten Kontur verglichen. Werden Abweichungen festgestellt, greift „SHAPEControl“ auf einen Korrektur-Algorithmus zu, der die Formpresse mit einem adaptierten Eintauchwert für den Folgeschritt versorgt. Auf diese Weise entsteht ein Regelkreis aus Messung und Korrektur, der zu einer optimierten Einformung jedes einzelnen Rohres führt.
Der angesprochene Korrektur-Algorithmus muss selbstverständlich die aktuellen Maschinenparameter – insbesondere Werkzeug-Radius und Unterwerkzeug-Abstand – berücksichtigen, um sinnvolle Korrekturwerte ermitteln zu können. Daher besteht eine ständige Kommunikation des SHAPE-Systems mit der Maschinensteuerung zum Austausch wichtiger Prozessgrößen. Eine eigene Datenbank ermöglicht dem SHAPE-System einen schnellen Zugriff auf zuvor berechnete Datensätze und bietet dem Bediener einen komfortablen Einblick in vorhandene Produktionsrezepturen.
In der Praxis bewährt
Umfangreiche Versuche an einer Laboranlage der SMS group in Mönchengladbach konnten die Funktionsweise der Regel-Algorithmen und die korrekte Datenverarbeitung im gesamten SHAPE-System nachweisen. Seit Abschluss der Versuche in der Laboranlage konnte das gesamte System bereits mehrfach für den industriellen Einsatz verkauft werden. Die erstmalige Inbetriebnahme bei Corinth Pipeworks bestätigt die hohen Erwartungen. Schon vor Installation des „SHAPEView“-Systems lieferten die Offline-Berechnungen verlässliche Prozess-Parameter zur unkomplizierten technologischen Inbetriebnahme der Formpresse. Die SMS group bietet seinen Kunden mit der Shape- Technologie ein Werkzeug an, um den ständig wachsenden Marktanforderungen an Qualität ohne Einbußen in der Produktivität gerecht zu werden. Die Shape-Technologie ist so konfiguriert, dass sie auch nachträglich in bestehende JCO®-Rohrformpressen eingebaut werden kann.