Closing the loop and helping battery supply chain participants to decarbonize.
Primobius GmbH is an incorporated joint venture between SMS group and the Australian company Neometals Ltd, to commercialise an efficient, environmentally-friendly recycling solution for end-of-life and scrap lithium-ion-battery (LIB) cells. Primobius has developed the process to use finite resources more efficiently and create a battery/EV circular economy based on ethical supply and reduced carbon footprint.
Primobius will recover all the LIB constituent materials with a two-step recycling solution for re-use of the products, which will include generation of high-purity cathode chemicals for the battery supply chain. Primobius will help to "close the loop" with a unique and sustainable method of recovering valuable lithium, nickel, cobalt chemicals, and other materials, from expended and scrap electric vehicle, stationary energy storage and consumer electronics LIBs.
Recycling of cell production scrap and end-of-life lithium-ion-batteries
Primobius is developing a sustainable recycling solution that targets the recovery of battery materials that are contained in production scrap and end-of-life lithium-ion batteries (LIBs), materials that might otherwise be disposed of in landfill or processed in high-emission pyrometallurgical recovery circuits. The Primobius’ process flowsheet targets the recovery of valuable materials from consumer electronic batteries (devices with lithium cobalt oxide (LCO) cathodes), and nickel‐rich EV and stationary storage battery chemistries (lithium‐nickel-manganese‐cobalt (NMC) cathodes). The LIB Recycling Technology is designed to recover cobalt, nickel, lithium, copper, iron, aluminium, carbon, plastics and manganese into saleable products that can be reused in the battery supply chain.
Two-stage recycling process
Stage 1 | Shredding and sorting
As a first step, the plant shreds spent batteries of different sizes and types, then sorts the plastic and metal components from the so-called "black mass". The two-stage shredding process is followed by drying and beneficiation to separate coarse metal and plastic materials from feed for processing in the hydrometallurgical section of the plant. The black mass product from Stage 1 contains the active materials for the operation of batteries. During the following hydrometallurgical processes, it is possible to extract from these active materials lithium, nickel and cobalt in a suitable form for reuse in making battery cathode materials.
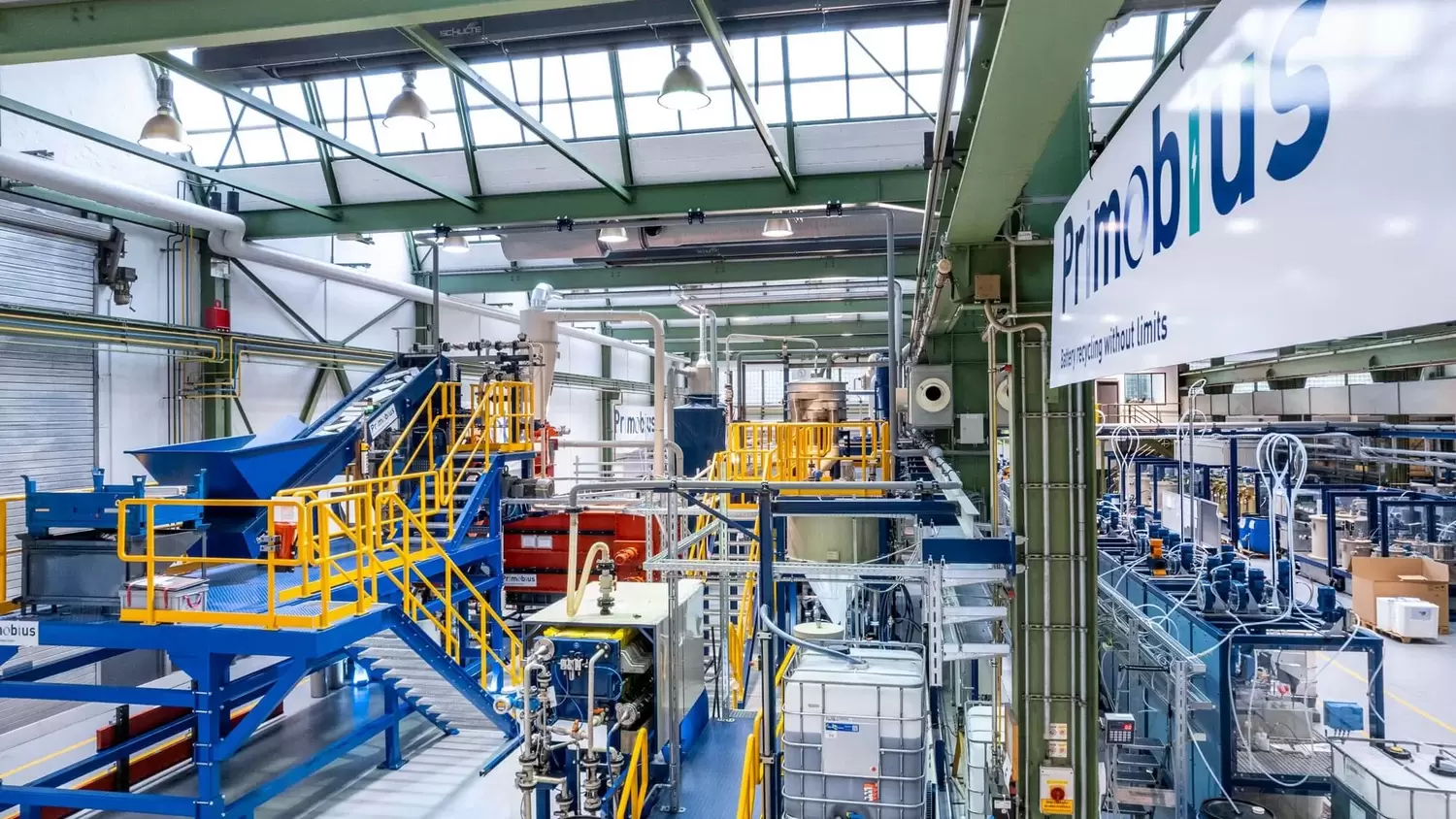
Stage 2 | Hydrometallurgical refining
The feed to Stage 2 (black mass) is processed in the leach circuit to extract cobalt, nickel, manganese copper and lithium. The pregnant leach solution (PLS) is separated from the solid leach residue. Further purification of PLS results in the recovery of cobalt and nickel as high purity sulphates suitable for potential sale directly back into the LiB supply chain. The recovery of lithium as a sulphate will enable its conversion to either lithium hydroxide or lithium carbonate and re-use in batteries. The manganese and copper sulphates are saleable to existing refineries of these metals or for direct industrial use.
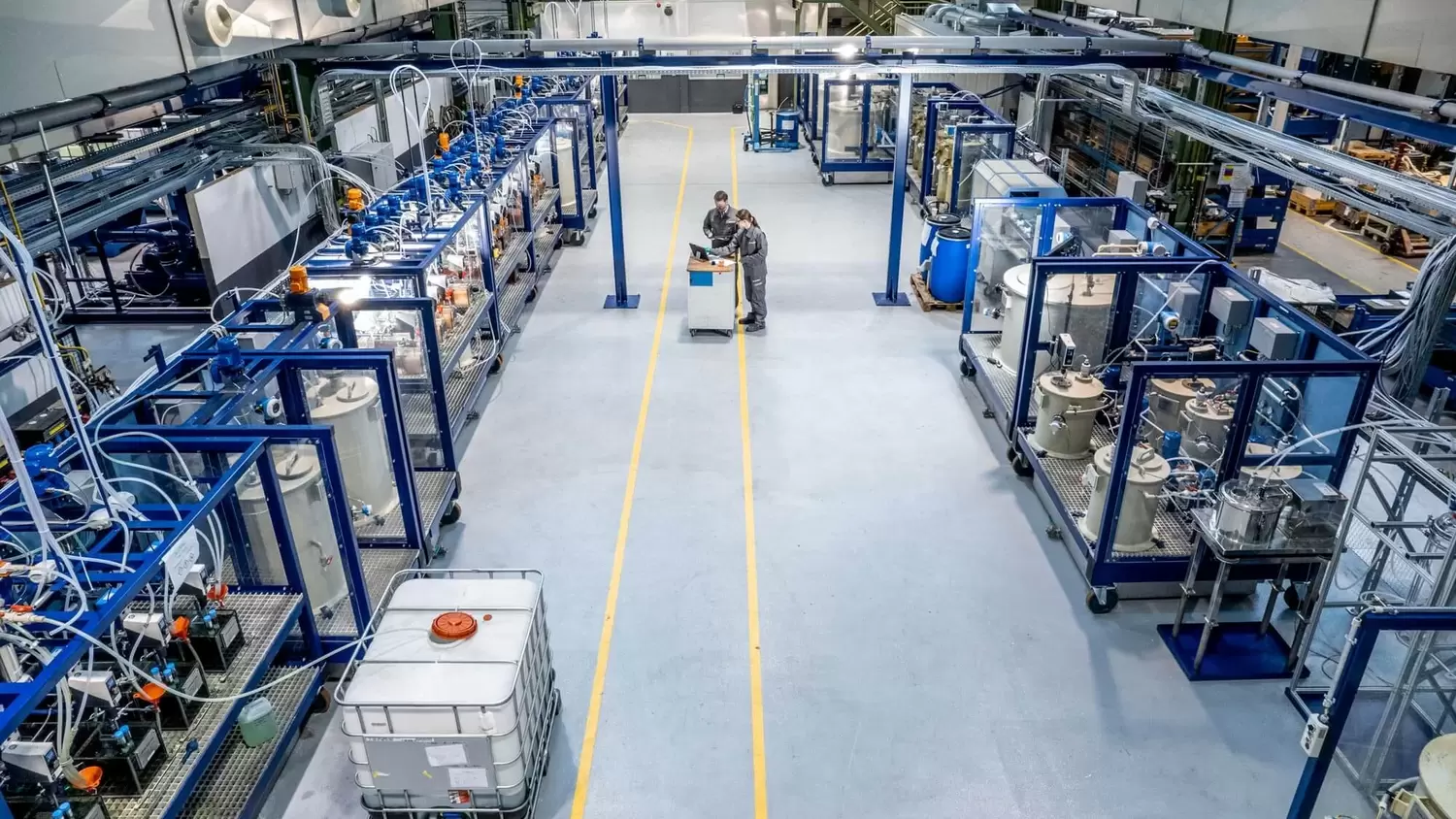
Responsibly-sourced high-purity chemicals
The two-step system consisting of shredding and recovery facilitates the efficient organization of decentralized and central system parts into a hub-and-spoke system. From this Primobius will generate both low and high value saleable products for re-use in new applications.