Electric steelmaking can save up to 90% of CO2 emissions compared to producing steel from virgin material in the blast furnace–BOF route. Given the dependence on the availability of scrap as a resource, predictions say that the share of scrap-based electric steelmaking will grow from around 20% today to more than 35% by 2050. Since electric arc furnaces can also process direct reduced iron (DRI) and hot briquetted iron (HBI) from direct reduction plants, electric arc furnaces (EAF) will make up for over 50% of steelmaking capacity by 2050.
However, EAF also vary widely in terms of their efficiency and power consumption. Here, it is important to consider not only the metallurgical vessel, but also the overall system including the power supply, particularly when using renewable energies.
Why the DC EAF is more energy efficient
The expected growth in electric steelmaking over the next few decades will naturally entail substantial investments in new EAFs. Therefore, every steelmaker should have an answer to this simple question: what is the best technology for my steel plant? AC (alternating current) or DC (direct current) technology?
There are many direct and indirect factors that influence a response to this, as well as, fortunately, some evidence too. In the last few years, many steelmakers have opted for DC furnaces thanks to the many advantages they offer.
First, the SMS DC EAF is more energy-efficient than the AC EAF due to the natural stirring effect, which provides temperature and chemical homogenization for a reduced “power-on” time. With a longer arc compared to the AC design, it increases the heat transfer and reduces electrode consumption too. In addition, flicker is reduced, which means lower capital expenditure for power compensation and less maintenance. The bottom electrode pin designed by SMS offers an extended lifetime (up to 2,000 heats) with limited handling costs.
Looking at all factors together, the operating costs of a DC furnace are lower than an AC, and CO2 emission rates are also lower. Finally yet importantly, the operator environment is enhanced, and noise levels during operation are under 40% compared to the AC design.
X-Pact® AURA for DC furnace feeding
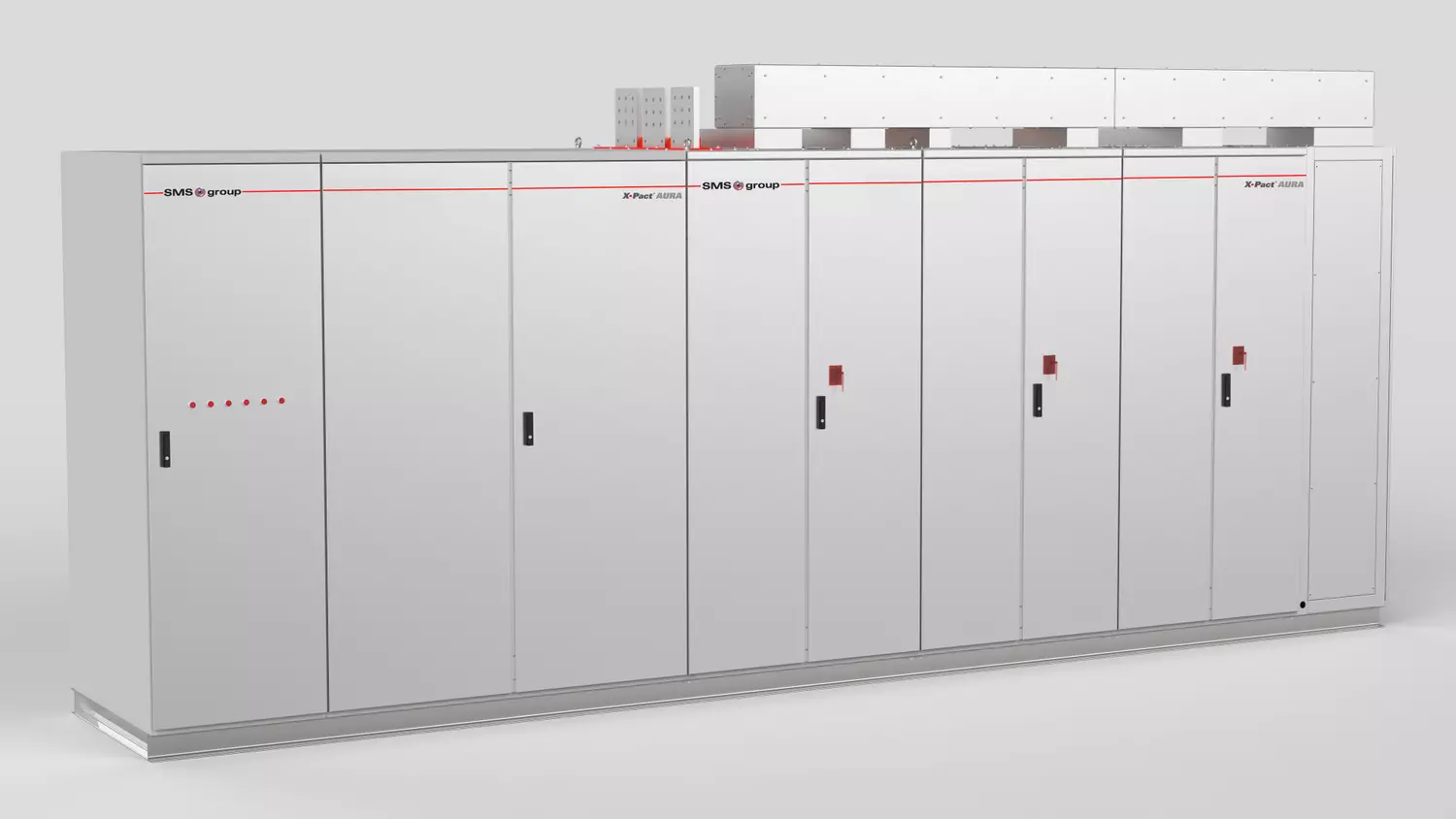
Furthermore, the goal of sustainable and energy-efficient production and reduced OPEX is also driving our customers to replace conventional EAF power supply systems based on a thyristor-controlled rectifier with feeding solutions based on advanced IGBT (insulated gate bipolar transistor) power electronics. The grids in existing production sites that use the integrated route are often not powerful enough to cope with a conventional EAF.
The new family of IGBT-based electronics modules, called X-Pact® AURA, boasts a completely modular concept, and the state-of-the-art power electronics technology guarantees maximum efficiency and power density. The new design achieves world-class performance in terms of current stability, dynamic response, efficiency, reliability, redundancy, and minimal impact on electric network quality.
The X-Pact® AURA platform provides a common, modular approach for DC furnace feeding. The chosen topology includes a multi-pulse diode bridge rectifier, a common DC bus, and an IGBT-based chopper stage. The rated power ranges from five to 350 MVA, depending on the power and number of modules. The use of innovative modulation techniques and proprietary control algorithms ensure a maximum power transfer with minimal impact on grid power quality.
Compared to the conventional thyristor-based DC design, X-Pact® AURA offers customers an unprecedented improvement in the key power quality parameters: a power factor above 0.95 and 30% flicker reduction.
The IGBT-based X-Pact® AURA system “cleans” the load of the furnace and enables the installation of a high-power melting unit within a weak grid environment.