The steel industry stands at a crossroads: Its products are indispensable for all modern societies. However, its current production processes need to be adapted in order to drastically reduce greenhouse gas emissions to limit climate change.
In order to support our customers on their path towards decarbonization even more efficiently, we have fully integrated Paul Wurth – the global leader in blast furnace technology - which has been part of SMS group since 2012. Together, we can focus on metallurgical challenges and on advancing hydrogen technologies. In addition, SMS group boasts considerable expertise in direct reduction plants, environmental protection solutions and recycling technologies. We place special emphasis on the development and implementation of technologies promoting CO2-neutral steel production. Both companies can build on 150 years of experience each in their respective fields.
Full range of decarbonization technologies for brownfield and greenfield projects
In general, there are considered to be three main routes to produce high-quality low-carbon steel at scale, using significant amounts of virgin material while still being able to process scrap in order to reduce the carbon footprint depending on final product specifications. SMS group is in the unique position to supply fully integrated solutions and leading technologies from iron ore to final products on all three routes. This is particularly important, as there is no one-size-fits-all ‘best’ option.
Local conditions have a huge impact on the economic viability and feasibility of each of the routes. Many decarbonization options rely on the availability of large amounts of – preferably low-carbon – electrical energy and, occasionally, on an appropriate short circuit power. Other factors, such as raw material availability and local policies, rules and regulations play a major part in technology selection.
- In new, ‘greenfield’ facilities, the key to reducing greenhouse gas emissions to below 100 kg CO2 per ton of hot rolled coil is the combination of green hydrogen, direct reduction and the electrification of all downstream processes.
- In existing integrated steelworks – also called ‘brownfield’ sites - we can enable the transformation of assets and infrastructure step-by-step – with significant potential to replace carbon-based fuels. This process requires the ongoing reassessment and reorganization of energy balances and flows. As a full liner, SMS group and Paul Wurth have the integrated solutions to bring about this change. Using this approach, we can develop a roadmap for all of our customers on their way towards carbon-neutrality.
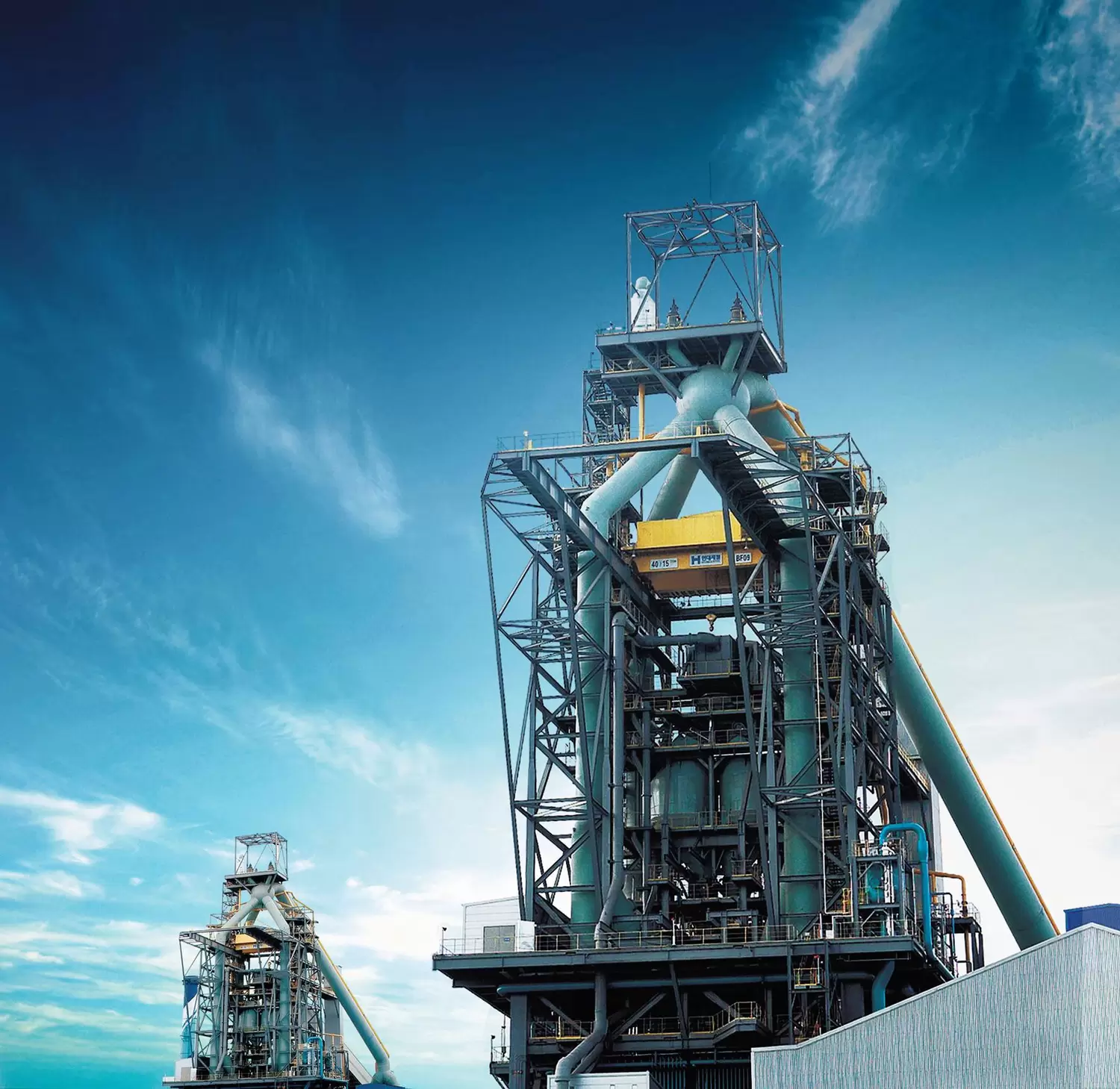
The roadmap to climate-friendly iron and steel production
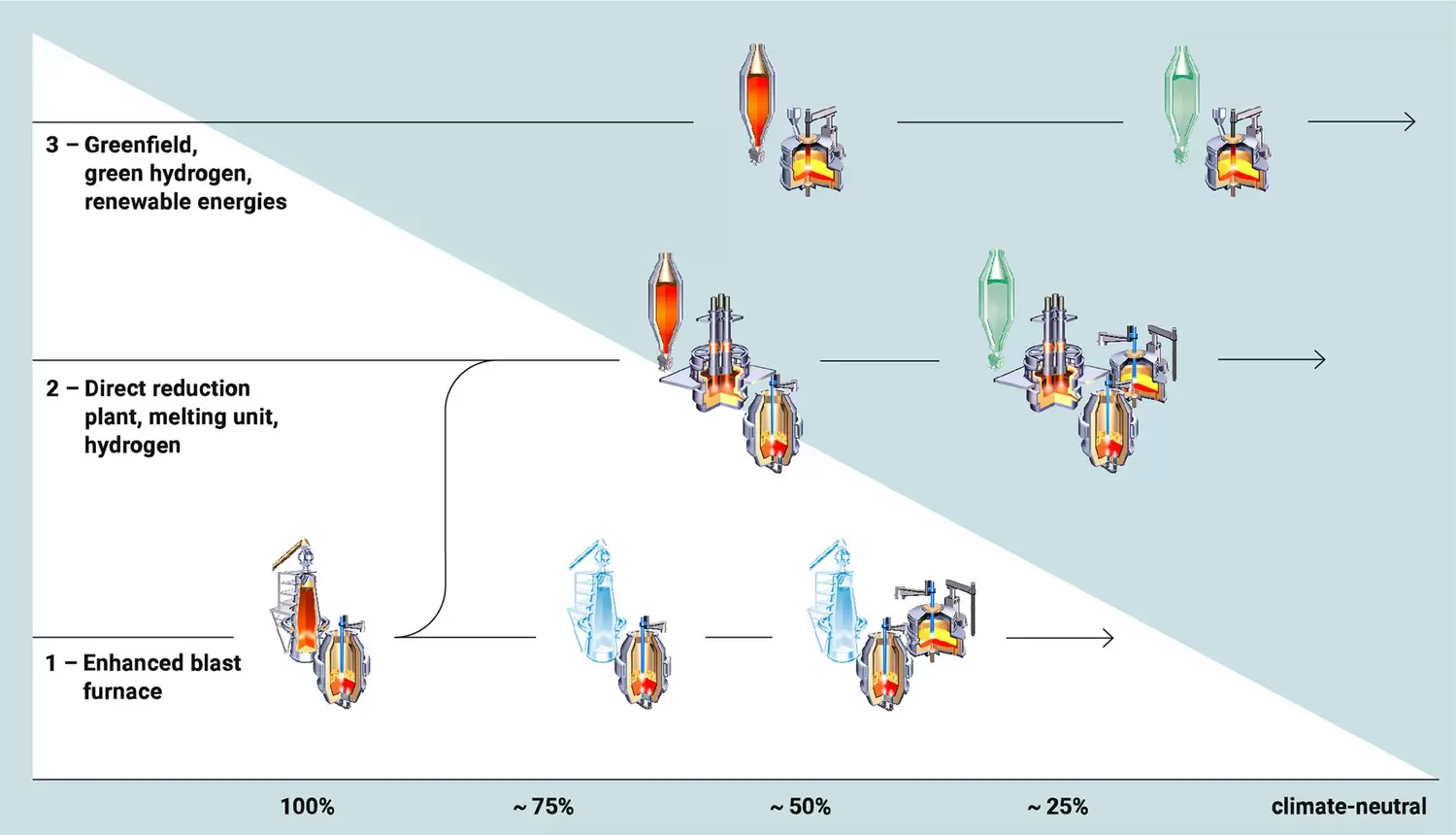
Brownfield project: "Blue" blast furnace and BOF converter
The integrated Blast Furnace-Basic Oxygen Furnace (BF-BOF) route uses large amounts of iron ore – in many cases, ore with only low iron content (typically 65% Fe or les). In this process, also known as the ‘primary’ route, limited quantities of scrap (about 20 percent) can be added during the BOF process. Due to the use of large amount of coke for iron ore reduction, the BF-BOF route is the steelmaking route with the highest CO2 emissions.
Technology painstakingly developed by Paul Wurth provides a substantial enhancement of both blast furnace and coke-making processes, reducing the coke rate to as little as 200 kg per ton of hot metal, with reduced CO2 emissions as a result.
In order to maximize the scrap rate, electric arc furnaces or, for example, the SMS CONPRO technology, can be used in the steelworks. This approach is limited only where by specific product quality requirements that may rule out the use of lower quality grade of (potentially contaminated with Cu, Sn, Ni, Mo) scrap.
Brownfield project: Direct reduction with OBF and BOF converter
In this route, the blast furnace is substituted by a combination of the MIDREX® direct reduction process and an Open Bath Furnace (OBF). Initially, it is possible to run the direct reduction process on a natural-gas basis and with the use hydrogen in place of natural gas at gradually higher rates.
The OBF, created by our SMS group subsidiary Metix, is similar in design to a conventional Submerged Arc Furnace (SAF) operated in a so-called ‘brushed arc’ mode. Here, we count on several hundreds of references for these kind of furnaces. The main feedstock on this route remains BF-grade iron pellet, while scrap can again be added in the steelmaking plant. One noteworthy advantage is the ability to add iron bearing wastes (up to 3 to 5% of overall charge), such as BF and BOF dust, mill scale and others within the smelter.
When integrating this route into an existing integrated plant, SMS’s and Paul Wurth’s respective 150 years of experience in iron- and steelmaking are a valuable asset when designing the interfaces and maximizing emissions reduction while maintaining, or even boosting, competitiveness.
Greenfield project: Direct reduction – Electric Arc Furnace
In a greenfield project and with green hydrogen available at competitive prices in sufficient quantities, a completely different approach can be adopted. Pre-reduced DR grade iron ore pellets from a MIDREX® shaft are hot charged into an electric arc furnace. No intermediate step is required and – depending on the specified final grade – only minor carburization is needed to reduce the nitrogen in the steel. From the very beginning, scrap can be added to the furnace at higher rates, with only the quality requirements of downstream processing stages setting an upper limit here.
Due to the immediate connection of all facilities, this route has the potential to come closest to carbon neutrality. This is especially so when the lean concept is extended downstream with a highly efficient CSP® or CSP® Nexus plant, which is a combined thin slab casting and direct rolling plant.
Best decarbonization roadmap for any given case
These three pathways represent the major options for decarbonizing primary steelmaking today. The pathways can be mixed, combined or modified to meet specific requirements.
However, all the options are subject to limitations. Each has individual strengths and weaknesses. Consequently, it is very important to study carefully the conditions for each case in order to choose the best relation between carbon efficiency and competitiveness. As SMS group has experience and references in all the presented technologies and processes, we are in a unique position to evaluate the best-suited roadmap for any given case.