In an interview with the magazine Prozesswärme, Prof. Hans Ferkel, Chief Technology Officer of SMS group GmbH, talks about the impact of hydrogen in the field of metallurgical plant engineering and how SMS group is positioning itself in the competition for the best solution to CO2-free steel production.
At the METEC 2019 press conference you announced that the first CO2-free slab will be produced using SMS group equipment. When are you planning to achieve this goal?
Hans Ferkel: As fast as possible! Actually, it's basically feasible even today. There are two approaches you can take. The first is via recycling: existing steel scrap is melted in an electric arc furnace using green power, i.e. carbon-neutral power produced by means of regenerative energy. The other one involves the production of pig iron by directly reducing iron ore in a shaft furnace using the Midrex process - and green hydrogen instead of natural gas. The direct-reduced iron (DRI) produced in this way can then be further processed in the electric arc furnace. You can combine these methods in multiple ways, depending on the steel grades you want to produce.
How important is hydrogen for SMS group?
Hans Ferkel: Hydrogen plays a key role in green iron production and is therefore crucial for SMS group as a leading equipment manufacturer for the steel making and processing industry. A key requirement here is that, in addition to efficient production of hydrogen by means of electrolysis, also the required power is generated without carbon emissions.
How is the company positioning itself in the competition for the best solution to CO2-free steel production?
Hans Ferkel: Here we are pursuing a holistic approach. On the one hand, we supply equipment to produce DRI via gas reduction. The proven Midrex technology is our preferred choice here. Last year, our Luxembourg-based group company Paul Wurth commissioned the world's largest Midrex plant - of 2.5 million tons annual capacity - in Algeria in close cooperation with our customer. And, construction of another Midrex plant of the same capacity is already under way.
In order to provide our customers at the same time a solution enabling hydrogen production in the most efficient way, SMS group participates as investor in the start-up company Sunfire via our subsidiary Paul Wurth. We are convinced that high-temperature electrolysis (HTE) provides the best results. In contrast to conventional electrolysis techniques using liquid water, HTE uses steam. In many industries, including the steel industry, waste heat – in particular of low calorific value within the 150 and 250 °C temperature range – is usually lost to the atmosphere because it simply cools down unused. Often the transport of this waste heat - for district heating purposes, for example - is not rational for economic and ecological reasons. Nevertheless, this waste heat is ideally suited for the on-site generation of the low-pressure steam required for the HTE. Water in the vapor state requires much less disassociation energy than water in the liquid state. Thus, we achieve a twofold benefit: We exploit so far unused heat to boost the efficiency of hydrogen production by HTE to over 82 percent. Conventional electrolysis methods hardly achieve 60 percent efficiency, as these depend on the use of liquid water.
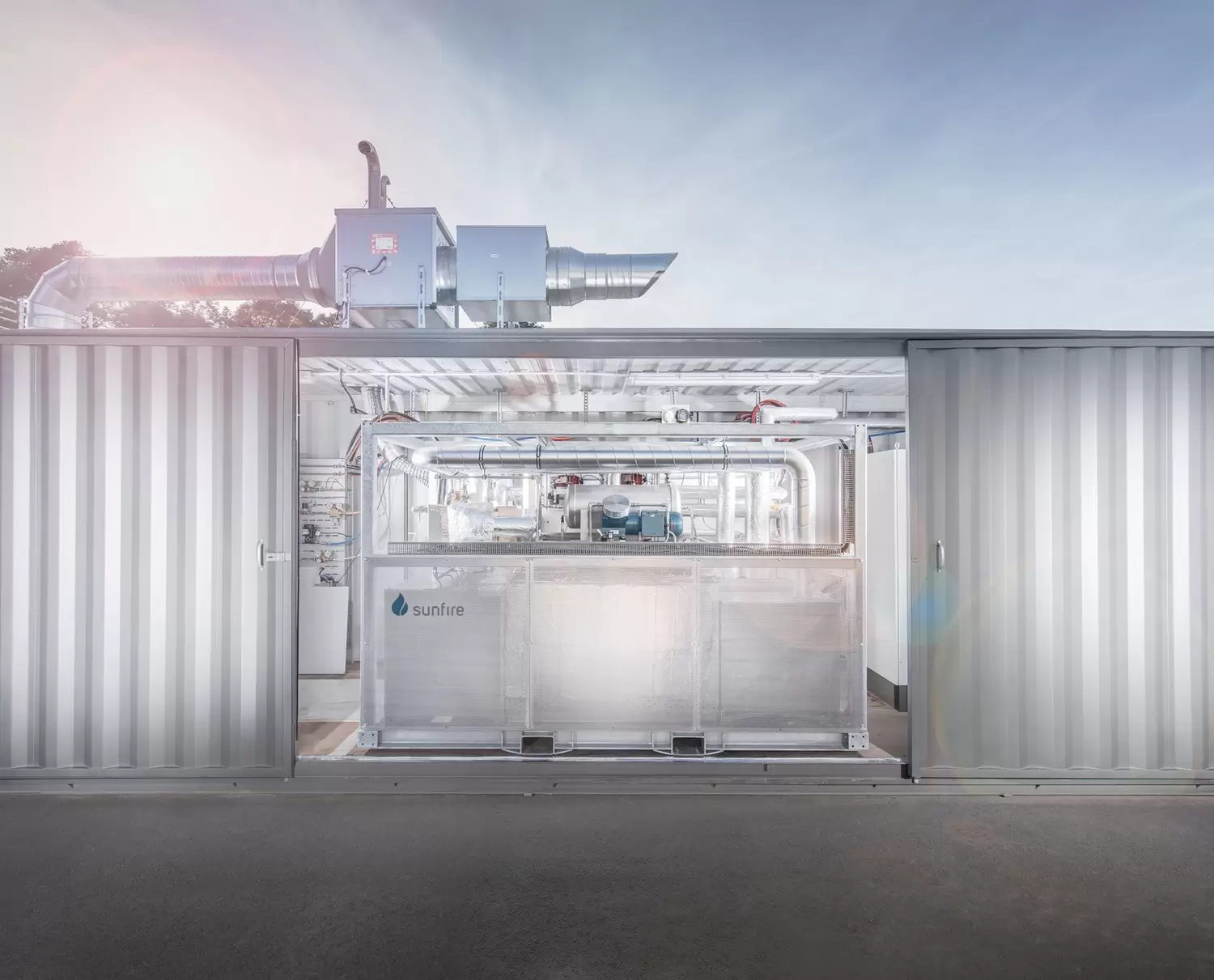
How is the technological transformation changing the metallurgical plant engineering sector?
Hans Ferkel: It will change the ironmaking process essentially. The classical blast furnace route with downstream oxygen steelmaking will be increasingly substituted by a combination of H2-dominated direct reduction processes, such as the Midrex process coupled with an electric arc furnace. Depending on what is technically and economically rational, the required hydrogen will be produced – preferably with green power generated in the plant itself or elsewhere – using the most efficient electrolysis method. With our solutions, this transformation can take place successively – meaning single selected blast furnaces can be substituted with green iron production. Here, the Sunfire technology enables us to take a modular approach.
At present, a standard hydrogen generation module has the size of a shipping container and requires around 740 kW of power. This corresponds to 200 Nm3/h of H2. With the Sunfire technology, you need approx. 300 MW to produce one million tons of DRI. We have already developed concepts for projects of this size. Most exciting about the Sunfire technology is that it can also be used for the electrolysis of CO2 to CO and O.
How can the costly transfer from the blast furnace route to hydrogen be financed by the steel industry?
Hans Ferkel: Steel is certainly system-relevant. This makes it crucial for the prosperity of the society and for the social market economy. Moreover, steel is 100 percent recyclable. Safeguarding the supply of steel – produced in an environmentally compatible way - is therefore a sociopolitical responsibility. It will be the duty of the state and politicians to create a financial framework that guarantees economic planning security during this transformation.
As a systems supplier, we are committed to supplying pioneering technology that frees the steelmaking process from its big CO2-footprint. I believe that every steel producer has to do his bit to safeguard our future.
Almost every steel maker in Europe has initiated pilot projects in this field. Do you think all steel manufacturers worldwide will follow the lead taken by Europe?
Hans Ferkel: That is difficult to predict. However, if the majority of states recognize that we need to fundamentally change the way we have been using our resources, this is likely to make also countries outside Europe take a different approach. Europe has realized the problem and is taking appropriate strategic action. Taking on this leading role opens up other opportunities. Since the last century, environmental technologies “Made in Europe” and “Made in Germany” have been much sought-after export goods. So why shouldn't this just as well be the case for highest-efficiency green steel production?
This interview was first published in the 3/2020 issue of Prozesswärme magazine. You can read the full interview here (German only).