One of world's largest industrial decarbonization projects
The move away from traditional blast furnaces at thyssenkrupp Steel’s mill in Duisburg has begun. From 2026, a new direct reduction plant operated with green hydrogen will take over part of the iron production process. It is one of the largest industrial decarbonization projects in the world – realized by SMS group.
Decarbonization of a brownfield site
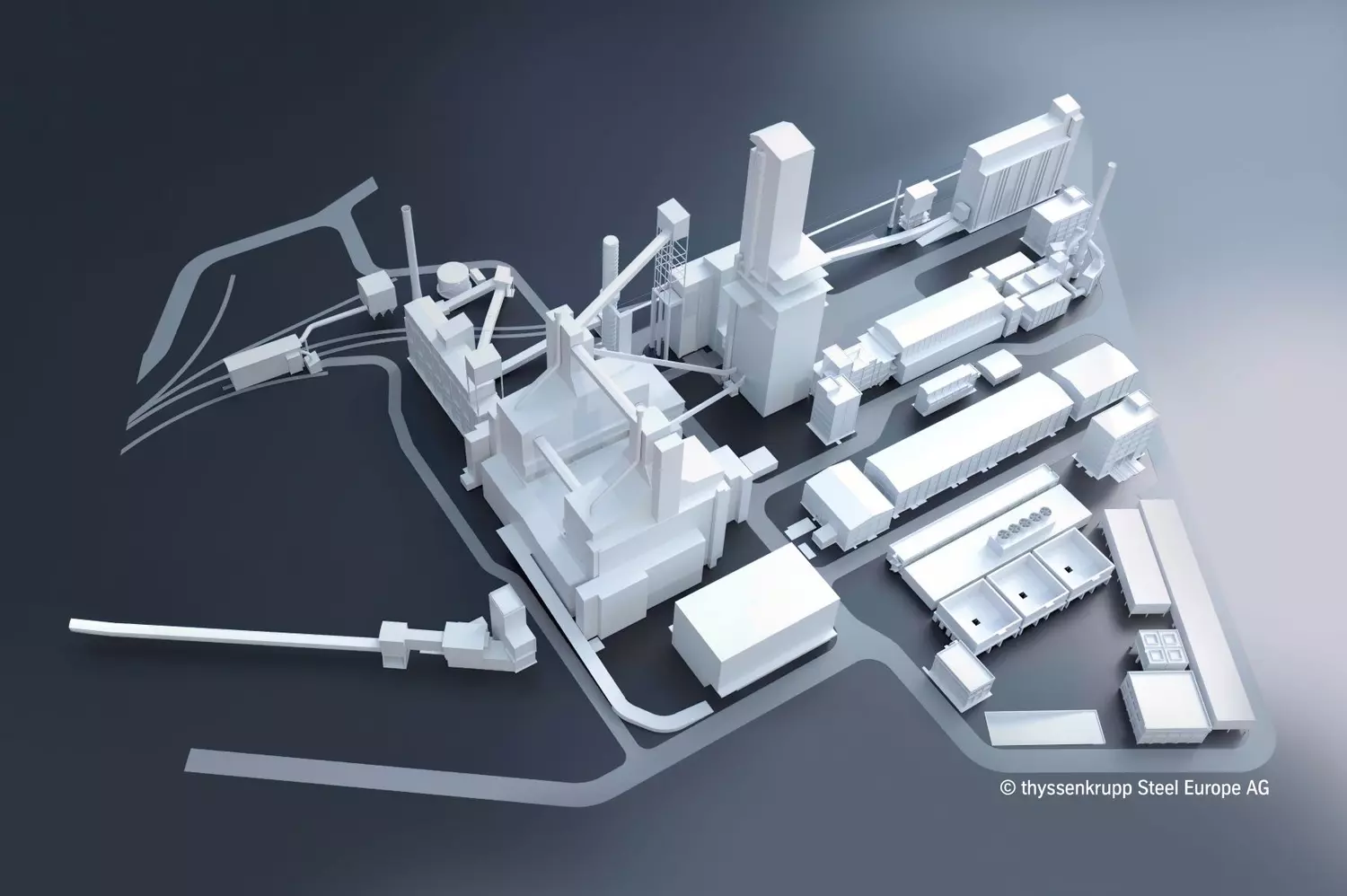
SMS group will realize a groundbreaking technological concept by combining a MIDREX® direct reduction plant and two innovative electric smelters for the production of 2.5 million tons of direct reduced iron (DRI) per year. This combination enables blast furnace technology to be replaced without the need to adapt downstream facilities from steelmaking to the finished product.
- The direct reduction plant is based on MIDREX Flex™ technology, which allows it to operate with any mixture of natural gas and hydrogen (up to 100 % hydrogen) with only minor modifications. The hot DRI will be directly charged into the electric smelters in order to reduce energy consumption.
- The electric smelters are also known as open bath furnaces (OBF). The name results from the fact that the bath around the electrodes must be kept free of metallic feed, in order to avoid contact between the electrically conductive DRI and electrodes. They are similar in design to conventional submerged arc furnaces. For these electrical reduction furnaces, we can rely on several hundred references, including the largest furnace in the world.
- The slag granulation system is based on the INBA® slag granulation process, incorporating our proprietary dynamic INBA® dewatering drum. The INBA® cold water process in conjunction with steam condensing granulation has officially been recognized as ‘Best Available Technology (BAT)’ under European Community directives. With about 300 reference installations, it is the most common and effective route for processing blast furnace slag in the world.
We are very pleased that we have SMS as our partner for the technological leap into hydrogen-based steel production. Together, we intend to demonstrate that an innovative and sustainable transformation of the steel industry is possible in Germany and Europe. We are thus creating the basis for tomorrow's green steel markets.
Advantages
- Flexible transition from natural gas to hydrogen
- Flexible use of input materials: MIDREX® furnaces can be operated with pellets or high-grade lump ore
- Consistently high product quality: Customers will continue to receive the complete, high-quality product portfolio with the same specifica- tions compared to the blast furnace process route
- Seamless integration and efficient use of existing steelmaking and downstream plants
- Production of blast furnace equivalent slag as a by-product for utilization in the cement industry as a clinker substitute
We are delighted that our technology, know-how and expertise in project management will support the green transformation at Germany's biggest steel producer. We all know: this is an important milestone on the road to a green metals industry.
News and links
Let's get in touch!