The integration of pickling and galvanizing processes, which are normally part of the complex route from hot strip to cold strip, into a single Pickling and Galvanizing Line (PGL) offers a green and economic approach to steel processing of hot strip, as the PGL gives the potential for reduced energy consumption and the possibility to produce 100% fossil free. In 2022, Wuppermann AG, together with the Fraunhofer Institute, has published a study about comparison of conventional galvanizing processes with the “heat-to-coat” process. The conventional galvanizing process typically involves heating the steel to around 750°C for recrystallization annealing, the gas fired heat-to-coat without recrystallization annealing process still to 600 – 650 °C, which can be energy-intensive and, if powered by fossil fuels, contribute to significant CO2 emissions. The “heat-to-coat” process as per SMS philosophy uses inductive, i.e., electrical, heating to bring the strip to the galvanizing temperature, which is around 450°C. Inductive heating is very efficient and is powered by electricity, which, depending on the source, can be generated from renewable resources, which results in fossil free production at Scope 1. Further combining investments and manpower of two lines in one, saves costs on the CAPEX and OPEX side.
We spoke with Nathanael Dischinger, Senior Sales Manager Flat Products Processing Lines and Qingjiang Zhao, Technical Sales Manager Automation, Digital and Service Solutions Flat Products/Processing Lines about SMS group’s “heat-to-coat” technology and about the economic and ecological benefits of the PGL’ plant and its process technology.
What makes PGL's system design unique and why should anyone use it?
Nathanael Dischinger: The “heat-to-coat” process as at Wuppermann AG, based on SMS group’s technology, excels with its high profitability, as all processes take place in a single facility. The process permits the production of galvanized hot steel strip with durable corrosion protection, an appealing visual appearance while still maintaining low production and investment costs.
A PGL bypasses the cold rolling mill complex in order to save the CAPEX and OPEX for cold rolled, annealed and galvanized cold strip, i.e. to create directly added value on the customers’ hot strip. The task is not only to capture the „simple application market“ but also to replace expensive coated cold strip with high quality heat-to-coated hot strip.
The PGL can create significant added value. We know from our reference customers that they have a cost advantage over the cold strip route of 50-70 USD/t. Just consider the savings for yourself if, for example, a PGL produces easily 500,000 t/year. As a result, one of our customers achieved a return on investment within 2 years.
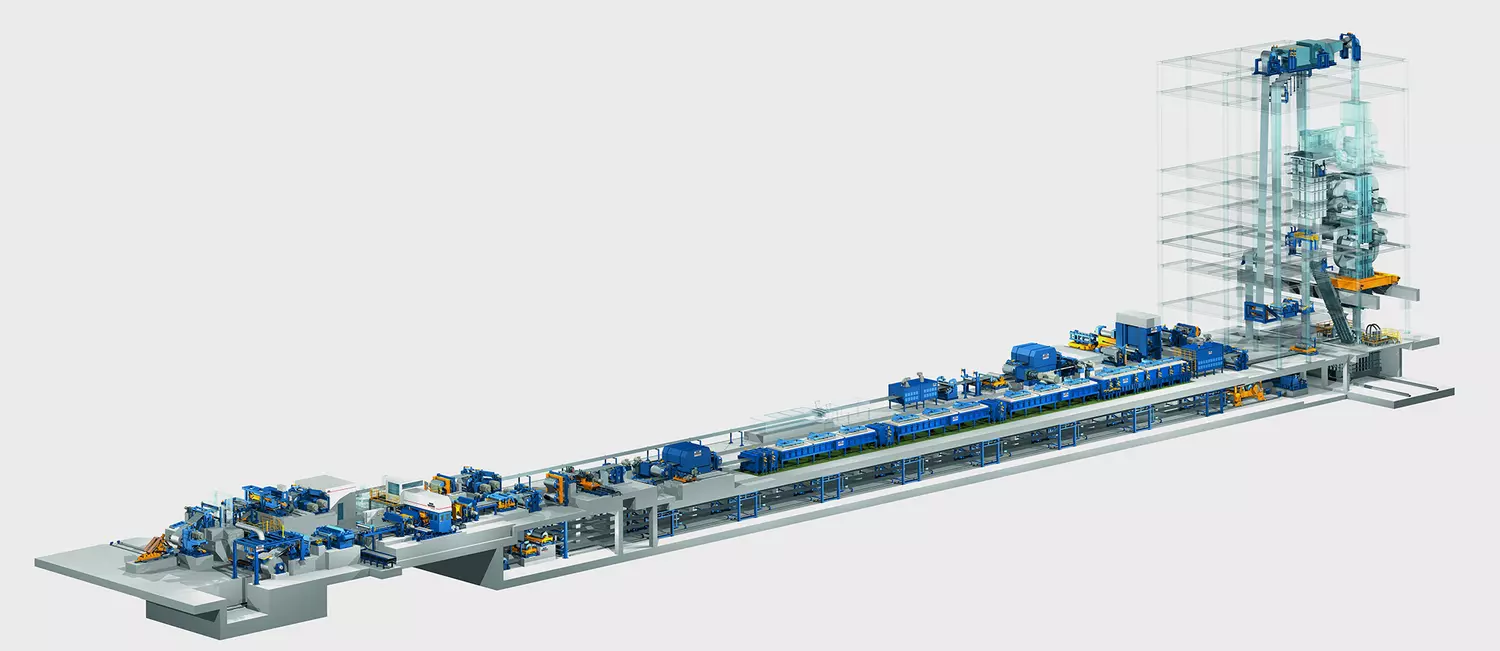
For which customers is this cutting-edge technology suitable, and what are the target markets?
Nathanael Dischinger: The PGL concept is particularly suitable for newcomers and investors who are not constrained by existing upstream routes and who think outside the box, by buying for example cheap hot strip on the worldwide market and put added value on of that.
However, the PGL line is also a cutting-edge technology for any of our traditional customers who have access to hot strip and staff capable of operating such a line. Typical products include those used in the furniture and building industry, agriculture, solar, partly automotive (inner parts), civil construction and various other applications. There is a growing tendency toward an increasing number of "heat-to-coat" products.
Which process technologies stand for the economic and ecological concept of the PGL?
Nathanael Dischinger: From the beginning, the PGL was designed with an electric inductive furnace. For more than 20 years, our customers have been making use of this proven technology. At the same time, SMS has gained 20 years of knowhow within inductive PGL technology, providing a unique advantage unparalleled by any of our competitors. The environmental friendliness of the process is largely determined by the CO2 balance of the electricity used, for example, from renewable sources. This is where the main leverage for reducing the CO2 footprint can be found. Additionally, the process can be 100% fossil-free. On top of that, the process is NOx free, which further supports customers in their environmental permit process.
How can electrical and automation solutions increase the energy efficiency of the line?
Qingjiang Zhao: As direct consumers of energy, electrics and automation solutions also contribute to the mission of CO2 footprint reduction by using energy „smartly“. For example, our X-Pact® Torque Drive, a highly efficient and compact mechatronic solution, enables the machine to achieve a total efficiency of 98 percent. This is made possible by the new design featuring an integrated toque drive. Consider a machine that is driven directly by a motor, without the traditional gearbox, similar to an electric car.
In addition to the ecological aspects, this drive concept offers particularly high effectiveness resulting from the elimination of losses caused by conversion stages and from the reduced need for ancillary equipment in the drive system. For our last project for one of our German customers, we conducted as a stress test of the motor in our SMS group workshop in Mönchengladbach, as usual, confirming that it is a proven technology we use for PGL and other types of processing lines.
Another example is our X-Pact® Drive low-voltage frequency converter, a modular drive solution for top-level production. Customers highly appreciate our spare parts service and the operator training we provide. In case of the torque drive, this system controls and drives the motor. In this way, SMS group offers customers integrated solutions that build lifelong partnerships.
Our newly developed “dynamic side trimmer” helps to optimize the trimming process. The strip width can be adjusted and optimized, resulting in significant energy savings. The system provides edge detection and positioning, so that scrap can be dramatically reduced to increase the productivity in the processing line. Our digital solutions are also part of this integrated solution and help to achieve energy savings by tracking and analyzing the data. The major savings originate upstream, for instance, in casting and hot rolling.
Are there other benefits of a PGL?
Qingjiang Zhao: Complementary benefits are achieved by adding two additional HS products to the portfolio. Producers are very flexible in meeting markets requirements (P&O or P&Coated production) when they can offer their customers this combination of pickled and oiled only, or pickled and galvanized strip. The inductive furnace, which I have already mentioned, is quite important as a feature and can be switched on and off for 1 hour. This makes it possible to manage heat-up or cooling down times and keep the intervals between production sequences very short. SMS group also offers a holistic modular solution for production planning – everything from a single source. This comprehensiveness sets SMS groups integrated solutions apart.
Last but not least, returning to our automation and digital solutions, the digital commissioning of automation equipment, which takes place in our test centers using the concept of a digital twin of the plant to simulate all complex processes of a PGL, significantly helps to ensure steep ramp-up of the line. The customer is involved in this process of integration testing right from the beginning of order execution. This approach ensures high levels of safety and quality from the start, meaning production can be started almost straight away, and smooth operation of the plant and a rapid return on investment can be achieved. The satisfaction of our customers speaks for itself.
What does your concept of integrated testing of automation involve?
Qingjiang Zhao: Every time we handle a project, our goal is to develop a common perspective and understanding of the project together with the customer. Our solution for the automation part of a project is the X-Pact® Plug & Work integration test, developed by SMS group for the digital commissioning of automation systems. During this test, all the hardware for the plant, such as controllers and control desks, is installed in the test field. Our engineers are divided into two teams: one focuses on the controlled object to simulate the line as realistically as possible, taking into account all movements and processes and the special technological features of the plant; the other team works on the control program that will be installed in the hardware.
With X-Pact® Plug & Work test, the original hardware and the software for the customer-specific plant are tested, pre-optimized in the test fields as a complex unit. The customer’s operators could also be trained in virtual but very realistic conditions. This concept of integration testing allows digital commissioning of automation under realistic conditions and shortens commissioning times by up to 30 percent.
Every customer project – both new plants and modernizations, benefits from the Plug & Work test. The pickling and galvanizing line for Nucor Steel Gallatin, Ghent, Kentucky, U.S.A., was one of our success stories with a very high level of customer satisfaction. Thanks to our Plug & Work concept, the commissioning on site went very smoothly. The customer’s operators and maintenance personnel built a relationship with the commissioning engineers during the integration test. This also made the startup process much faster.
It is certainly an advantage for customers to get everything from a single source as an integrated solution. In this context, which process automation solutions would you highlight?
Qingjiang Zhao: We use X-Pact® Turbulence Pickling Model to maximize productivity while minimizing energy and acid consumption. The model meets the requirements for optimal strip surface quality, minimized excessive pickling, lower maintenance and operating costs.
The pickling model enables flexible pickling of any desired coil sequence. It dynamically controls all relevant technological setpoints to achieve high product quality at maximum throughput. Process conditions are adjusted according to the requirements of each strip segment. Operators are relieved from time-consuming and error-prone tasks. All of this leads to significant savings in energy and resource consumption.
Additionally, with the closed-loop mass flow control, our skin-pass mill operates not only in temper mill mode but also acting as a rolling mill. Depending on the processed material, the reduction in energy consumption can reach more than 10%.
Can you short up: why PGL should be considered and by which producers?
Nathanael Dischinger: The use of galvanized hot strip is particularly attractive for applications where a galvanized cold strip would normally be used. Because a number of cost-intensive process steps are omitted from the production of galvanized hot strip compared to the production of galvanized cold strip, enormous cost advantages arise here, which ultimately increase the margins of the steel producer.
In order to increase the possibilities of a PGL further – particularly the flexibility – of first and foremost very thin materials, further modifications to the mechanical line concept are possible, depending on the availability of very thin hot strip (< 1.0 mm). Other suitable options are the integration of a second skin pass mill or reduction mill stand or an inductive annealing module.