The use of torque motors can reduce the energy consumption of closed-die forging presses by around 20 percent. After the successful implementation of this drive concept in 2015, new references will go on stream within the next months.
For years now, the demands paced on suppliers to the automotive industry have been heading in one direction only: Up; stricter emission standards, increasing performance requirements, and higher expectations in terms of driving comfort are making life difficult for manufacturers – and are also having an impact on business in upstream sectors. Musashi Europe is facing this challenge head on. For almost 100 years, the company has been supplying components for driveline and chassis technology. At its plant in Bockenau, Germany, Musashi soon plans to manufacture large, rotationally symmetric forgings on a new press that utilizes an innovative drive concept. A concept that was designed and built by plant engineering specialist SMS group.
Low speed, great effect
The first new press of this kind went on stream in 2015. The machine, which was actually developed for test purposes at the time, quickly found a buyer. Its energy consumption – which is easily confirmed after more than 25 million strokes – is around 20 percent lower than comparable conventional presses. To exploit potential like this to its full, SMS group started looking at new drive system options. This led to the idea of utilizing torque motors. A characteristic feature of torque motors is their very high torque at relatively low rotational speed. Used in the right application, they replace a conventional servo motor and its complex reducing gear.
"Our customers in the automotive supply sector are under tremendous cost pressure", explains Martin Scholles, Project Manager for Sales Closed-die Forging Presses at SMS group in Mönchengladbach. "They have to demonstrate savings on an ongoing basis – in most cases these can be between two and three percent every year." At the same time, however, their expenditure is increasing – for wages and energy, for example. That is why automotive suppliers are under particular pressure to reduce costs.
Concentrated knowledge
At SMS group, sales, technology, and design experts pooled their knowledge to find solutions to the problem and gain a vital edge over the competition. And it worked. "No one else has this torque drive for presses", adds Scholles proudly.
No one else has this torque drive for presses
At the first glance, the drivetrain of the press looks alike the drivetrain of a conventional press with a clutch and a flywheel. The special feature of the system is its type of acceleration. Instead of accelerating with the conventional friction clutch, it uses a torque drive, which is attached directly to the eccentric shaft. As soon as the shaft reaches the same speed as the flywheel, the clutch is engaged without any friction losses. The energy provided by the flywheel can then be used for the required forming work. After forging the clutch is released again. To decelerate the drivetrain, the torque motor is switched to generator mode. The energy is either fed back to the power supply net or charges the flywheel to bring it back up to speed. "In conventional presses, this energy would be lost but our press can use it again. In this way, we are now one step closer to perpetual motion," says Scholles.
The flywheel itself is also accelerated, maintained at speed and decelerated by a torque motor. This concept allows a swift startup and stop of the flywheel witch saves precious time when interventions at the tools are needed.
"The drive also separates motion sequences that, in the past, were necessarily performed in direct succession", remarks Scholles. "This gives us a greater degree of freedom, from which the customer can benefit." The time windows for transfers, for example, are longer as a result.
SMS group stands by flywheel concept
With the new press type, SMS group is standing by the design variant with built-in flywheel. "We firmly believe that this is still the most efficient way of providing energy", says Scholles. By contrast, the servo presses offered by our competitors have no flywheels. Their energy input, which can be in the megawatt range, needs to be supplied from the mains. This results in voltage peaks and in higher energy consumption costs with rival products. “Our system has also peaks, but they stay within the intermediate circuit of the inverter. It has no exceptional external impact, i.e. on the mains."
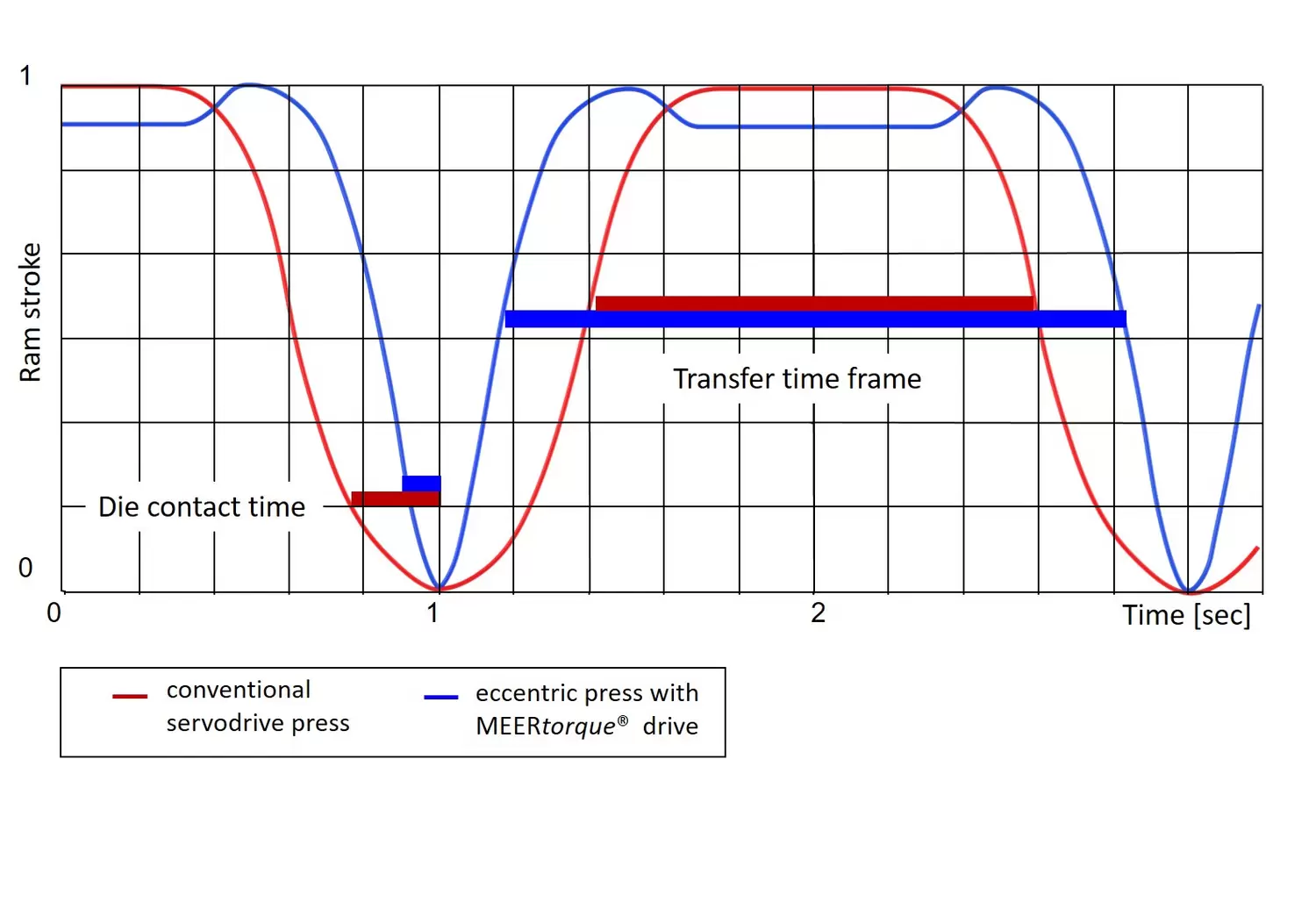
The idea for this "unconventional servo press" was born in 2014. With this machine, the goal – as well as improving efficiency – was to make it more maintenance-friendly and so reduce costs for the customer even further. According to Scholles, this works because the rate of wear is far lower with this system. Whole assemblies are no longer required, like the operating brake, for example; only the motor is used for braking. In addition, the clutch can be sized smaller shows virtually no wear, as the clutch is engaged when the eccentric shaft and flywheel are running at synchronous speed. Due to the use of the torque motors, all these advantages can be achieved while avoiding complex gearsets.