Automated forging lines often provide three to five stations where different stages of the forging parts are located. In most cases, as many spray heads are required as adapted in the nozzle arrangement to the loaded die zones. They are directed to the press area via linear feeders, robots or articulated cam-operated arms when the press has opened after a forging punch. The aim of an improved spraying technique is extending the service life of forging dies and saving spraying agents.
New design
By leading each of the three different ducts (atomizing air, spray medium and control air at a system pressure of 4 to 6 bar) to each nozzle a complex duct structure is provided. The particular design employed by SMS group (also see patent application WO 201712609 A2) is the result of a consistent implementation to provide function-carrying paths and chambers with constant wall thickness. It is a process which can be used in the meantime also for other SMS group component parts when flow technology components are additively manufactured. For spray heads the design turned out to be revolutionary during the development stage since it offers several advantages at the same time: low weight, flexible in designing and suitable for different materials. In order to make the elements more resistant the spray heads may also be manufactured from metal – without any constructive or geometric changes. This is a substantial advantage of the 3D spray head developed by SMS group.
Succesfully in use
Meanwhile, the spray heads have been successfully tested and employed at customers and most of the existing connections could be used. In continuous operation, the applied spray heads made of polyamide revealed a temperature of approx. 50 degrees Celsius operating without problems. Spraying pattern and handling were even superior to that of conventionally manufactured parts. Inner deposits which often occur when conventional spray heads are used were not ascertained. The reason for this lies in a flow-optimized duct routing to the nozzles. The operator Bharat Forge was highly satisfied with the use of the spray head and would like to establish this technology in future in his company. “In this way, we can protect the robots which otherwise are brought up to the maximum stress limit.”
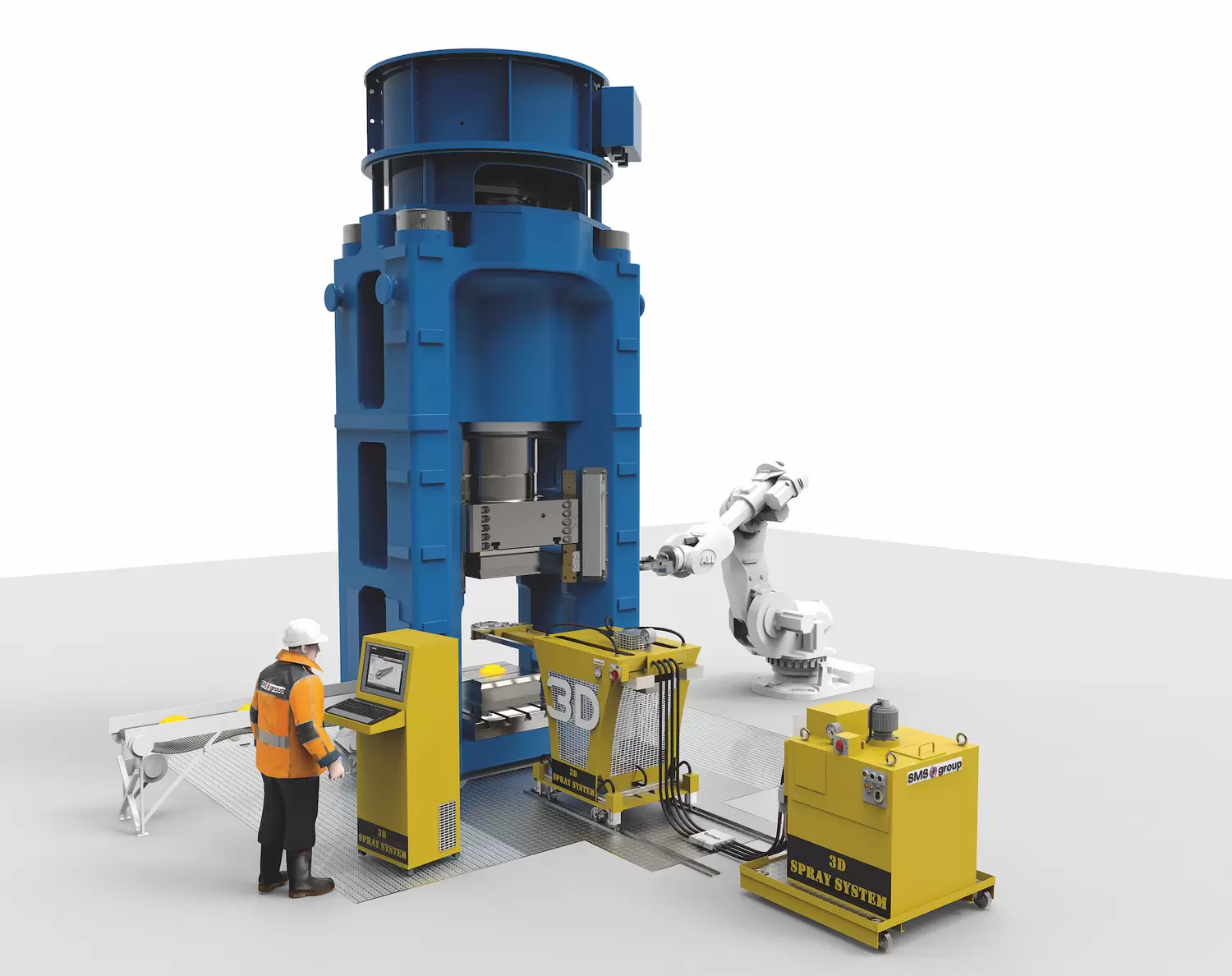
Spray heads made of plastic
The plastic spray heads should not be thermally overloaded. If the forgings come into contact with the spray heads protective measures have to be taken to make sure that the service life of the spray heads is not prematurely shortened. An immediate retraction of the spray arms and the triggering of emergency cooling with compressed air are recommended. Another big advantage is a low component weight. A 3D spray head made of plastic weighs only one tenth of a conventional spray head. Compared to a conventional spray head, a 3D metal spray head is still easily lighter by up to 70 percent. The accelerated mass is less ultimately enabling a higher cycle time of the usually automated processes. Eventually, manufacturing with additive technology in combination with this design is also energy efficient since only as much material as required is used.
Advice is also given as regards improvement potential. Since modifications of nozzle or angle positions do not entail much greater effort, a gradual approach can now be implemented: in an initial step, for example, spray heads can also be made of polyamide and then the same geometries be made of metal. At this point, a change of thinking has taken place which was initiated by 3D printing. The customer is free to choose. Although the spray head is the centerpiece of this technology, all these advantages are impossible without an optimally adapted periphery. SMS group offers a complete package to its customers which can offer subsequently even further advantages. It consists of three major blocks forming a single entity – spray technique, automation and control.
Close consultation with customer
It has been shown that the design of 3D spray heads is not very time-consuming. SMS group has developed a method where the positions of the nozzles are only determined and transmitted by the user which could also be marks manually added to a drawing or position indications in a table. Since the customers of SMS group are regarded as the best experts for their own products the positioning of the nozzles provided by the customer is primarily used. It goes without saying that the technologists of SMS group also take over the complete design of the die forging plant.
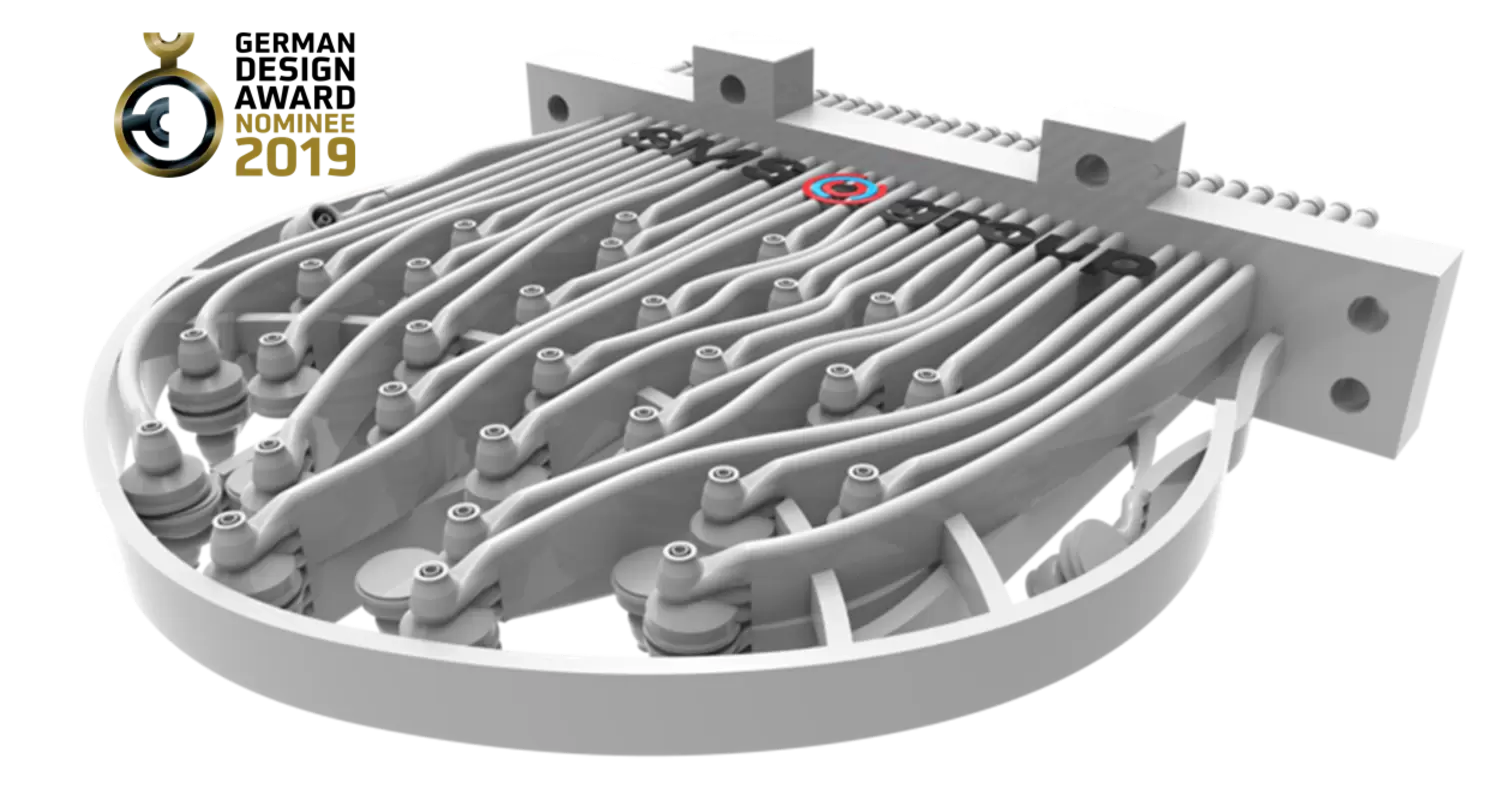
Spray technique, automation and control as single package
A fast supply of automation is in a linear fashion and is adapted to the lower weight of the load-bearing spray heads. The spray technique connected to the control system opens up a wide range of possibilities that have not been known in the spray technique of die forging plants to this extent. By additive manufacturing the degree of complexity for the manufacture is no longer relevant which also affects the control technology. It is not important for the user whether three or twenty nozzles are switched individually, in quick succession or in alternation. In principle, the actuation of each individual nozzle can be changed on the entry screen. To optimize the required quantity of the spraying agent, the process is permanently monitored by sensors. Current-carrying elements may also be provided directly in the structure during printing in the form of recesses. Whereas in the past, the setting of individual pressures and switching times had to be specified separately a simple and intuitive entry is now possible. What’s more, a standardized connection makes the replacement of 3D printed parts easier, safer and fast. Thanks to intelligent sensor systems, intuitive operation, analysis in real-time and permanent process optimization the 3D spray system gets fit for Industrie 4.0.