It represents a quantum leap in the productivity of PQF® (Premium Quality Finishing) plants for the production of seamless tubes. As market and technology leader and inventor of PQF® technology, the SMS group experts have succeeded in achieving a 30 percent increase in output with the fourth generation of PQF® plants. This gain is not only possible with new plants; existing PQF® plants can also fully benefit from this with a low-investment upgrade.
The fourth generation of PQF® plants – applicable both as a new plant and upgrade solution - is characterized by a considerable cost reduction per ton of tube and substantially higher profitability for tube producers, who are able to gain a significant competitive edge as a result. Achieving such a high production capacity and plant performance in the manufacture of high-quality PQF® tubes has not been possible until now.
Economic benefits and new market opportunities
For producers of seamless tubes, the increase in productivity certainly has positive effects. Here are two possible scenarios:
- Scenario a): A 30 percent higher production capacity with the same production time and manpower means an increase from 500,000 to 650,000 tons per year. This creates new opportunities for sales and a fast return on investment.
- Scenario b): The performance enhancement is used to produce the same quantity of PQF® tubes in less time than before. Due to the minimal time required, working shifts and human resources can be adapted accordingly.
Depending on the market situation and capacity utilization, plant owners can either produce more tonnage or a set target tonnage in a shorter time using the same manpower. In both cases, cost efficiency is higher and tube producers can respond adequately to volatile market and price situations.
PQF® – the standard of the future
Around 40 million tons of seamless tubes are produced worldwide every year, around half of them in high-grade PQF® quality. The main customer is the oil and gas industry, which uses OCTG tubes preferably made using the PQF® process. The reason: As the conditions for extracting fossil energy deposits become more and more extreme, the tubes must meet correspondingly high quality and load requirements. Structural tubes are another area of application for high-quality PQF® tubes. Here, further market shares can be gained through reduced manufacturing costs. Likewise, existing, old equipment for seamless tubes can be replaced by state-of-the-art, digitalized PQF® plants of the fourth generation, as conventional seamless tube lines cannot viably compete with the high-precision PQF® quality nor with the new productivity boost.
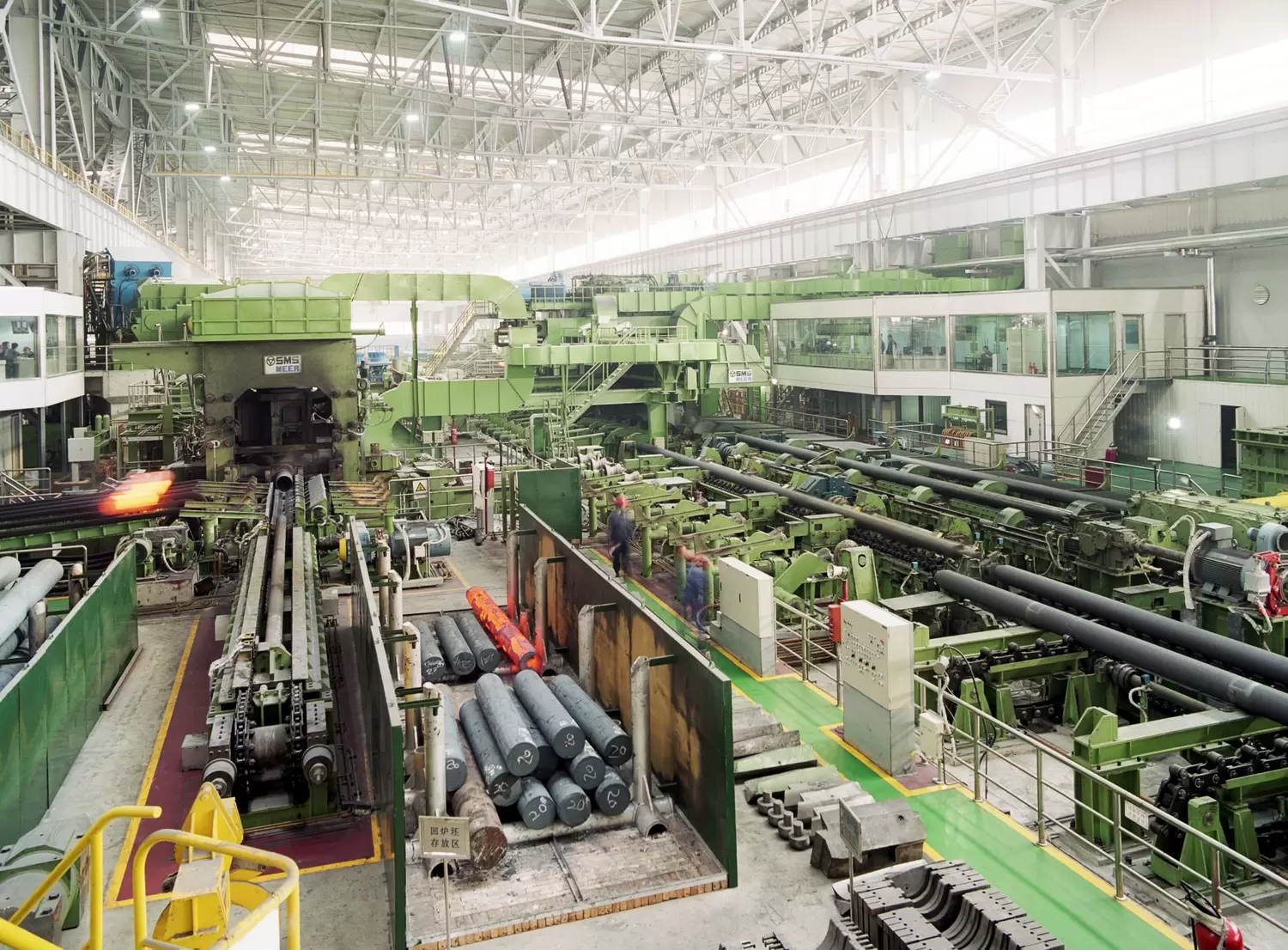
A plus for the environment
In terms of their lifecycle assessment and sustainability, plant owners also benefit from the fourth generation of PQF® plants. The reason is that the total amount of energy required does not increase – as one would otherwise expect – in direct relation to the growth in production. On the contrary, less energy is required per ton of tube produced. This mainly results from the fact that the energy consumption of the secondary operating facilities and administrative facilities remains constant with the increase in production.
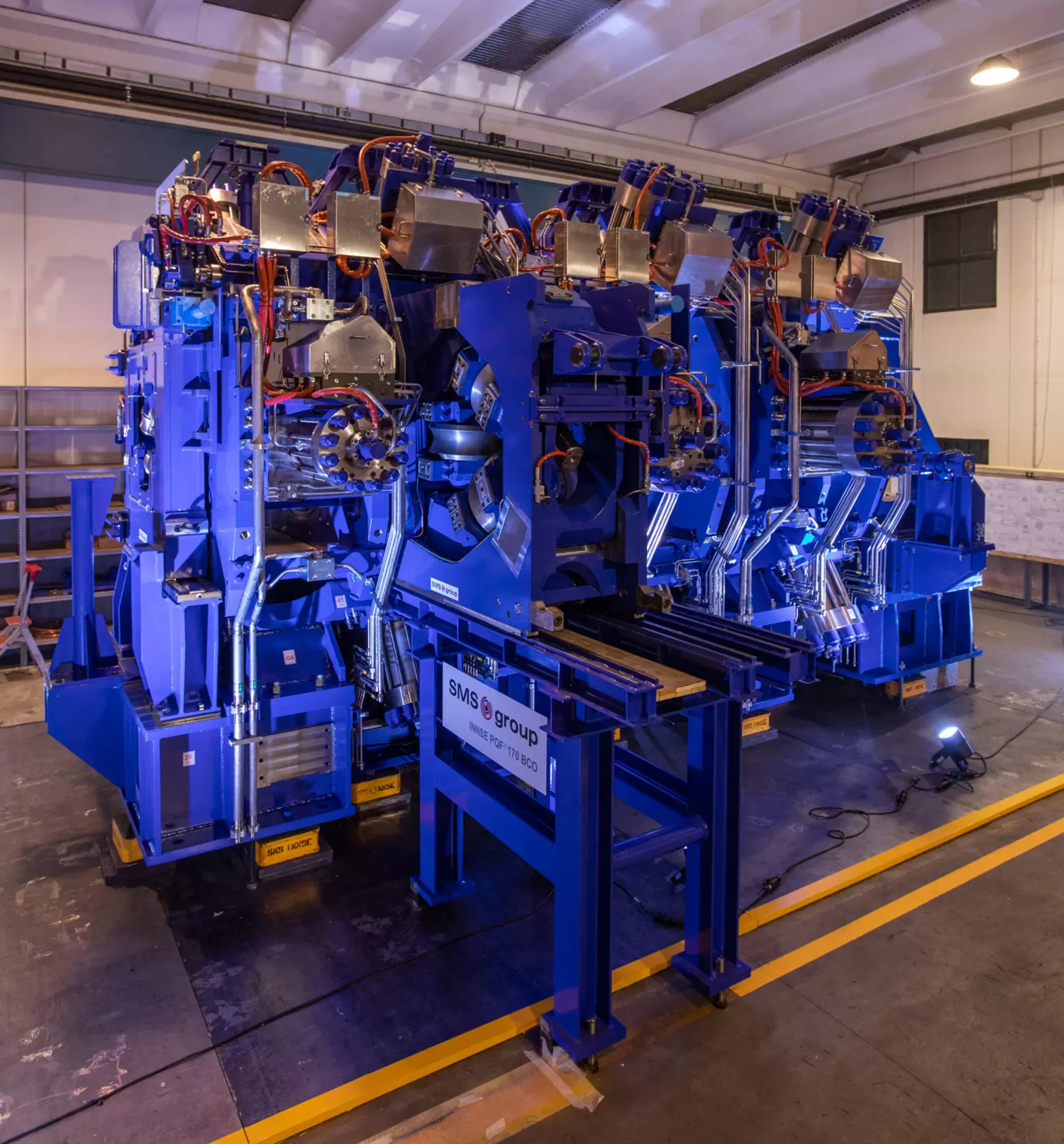
Significant five-second reduction in cycle time
The main innovations include the arrangement of a quick entry side with the inline insertion of the mandrel in the pierced billet.
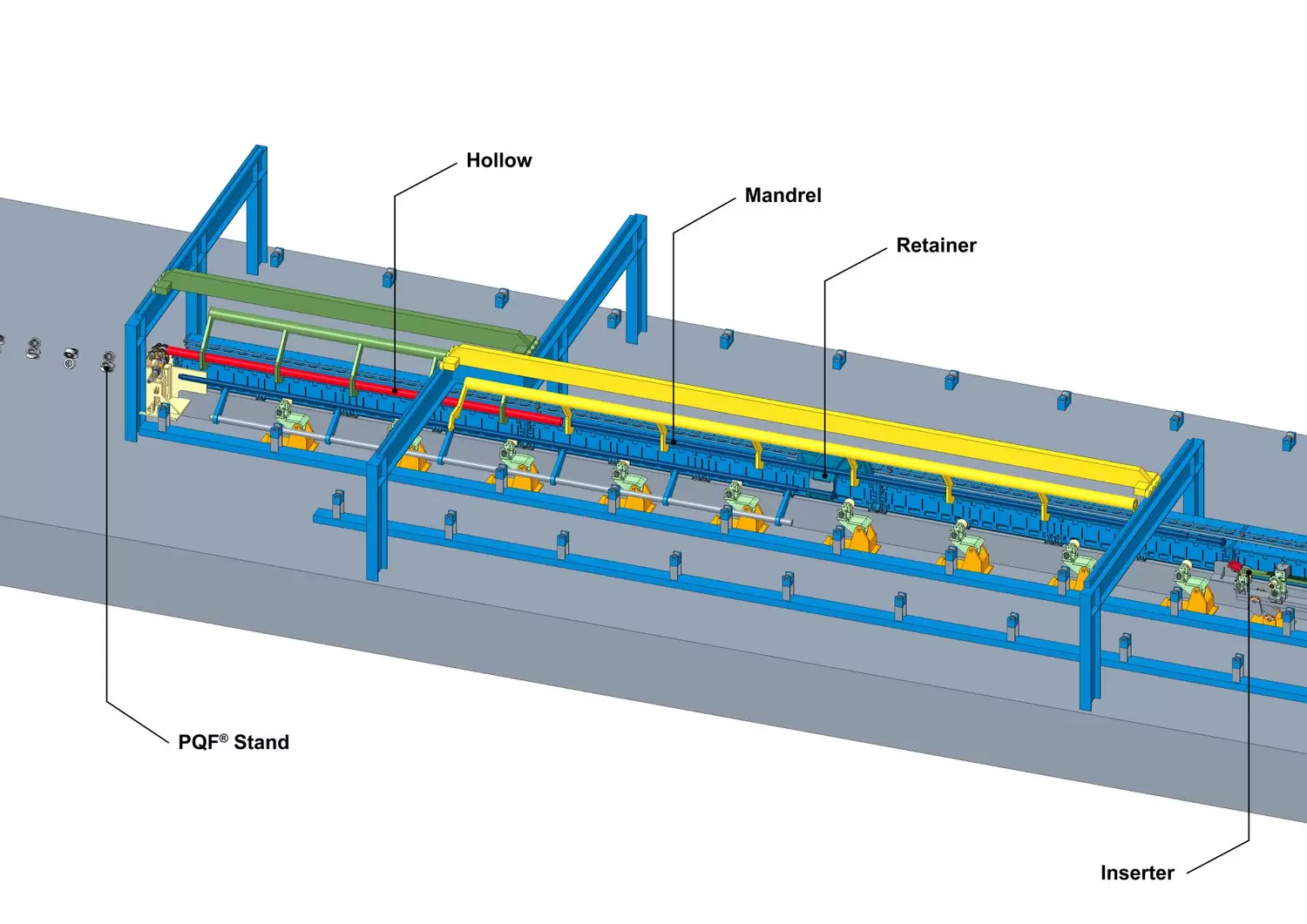
In conjunction with the highly efficient configuration of the retaining system, the cycle times are reduced by between four and five seconds. This means that a cycle time of around 20 seconds per tube – and even up to a peak of 18 seconds – is now possible instead of a cycle time of 24 seconds. A 7-inch PQF® is therefore able, for example, to roll 200 tubes per hour; a 10 ¾-inch PQF® can achieve 150 tubes per hour.
Another new feature is the chocks design in the PQF® rolling mill that help to simplify roll assembly and dismantling. The roll and shaft are separate from each other and are no longer made of one part. This reduces tool costs considerably and reduces the necessary operating stands inventory. A special, newly developed grooved profile between the roll and shaft replaces the previous cylindrical coupling ensures reliable torque transmission.
Higher speed also means higher productivity – but what effect does this have on quality? The consistently high quality and precision levels of PQF® tubes are ensured by the rolling technologies and performance module from SMS group. These include the advanced, digital inline technologies as part of Industry 4.0: For example, the CaliView® measuring system, developed by SMS group, enables the fast inline calibration of all longitudinal rolling mills and thus guarantees perfect alignment of the pass line. Equipped with the LASUS® Multiscan and SecControl® systems, the wall thicknesses of the tubes produced can be individually measured and controlled. Furthermore, CARTA® neo supports process engineers with the monitoring, analysis, and intelligent control of all quality parameters.
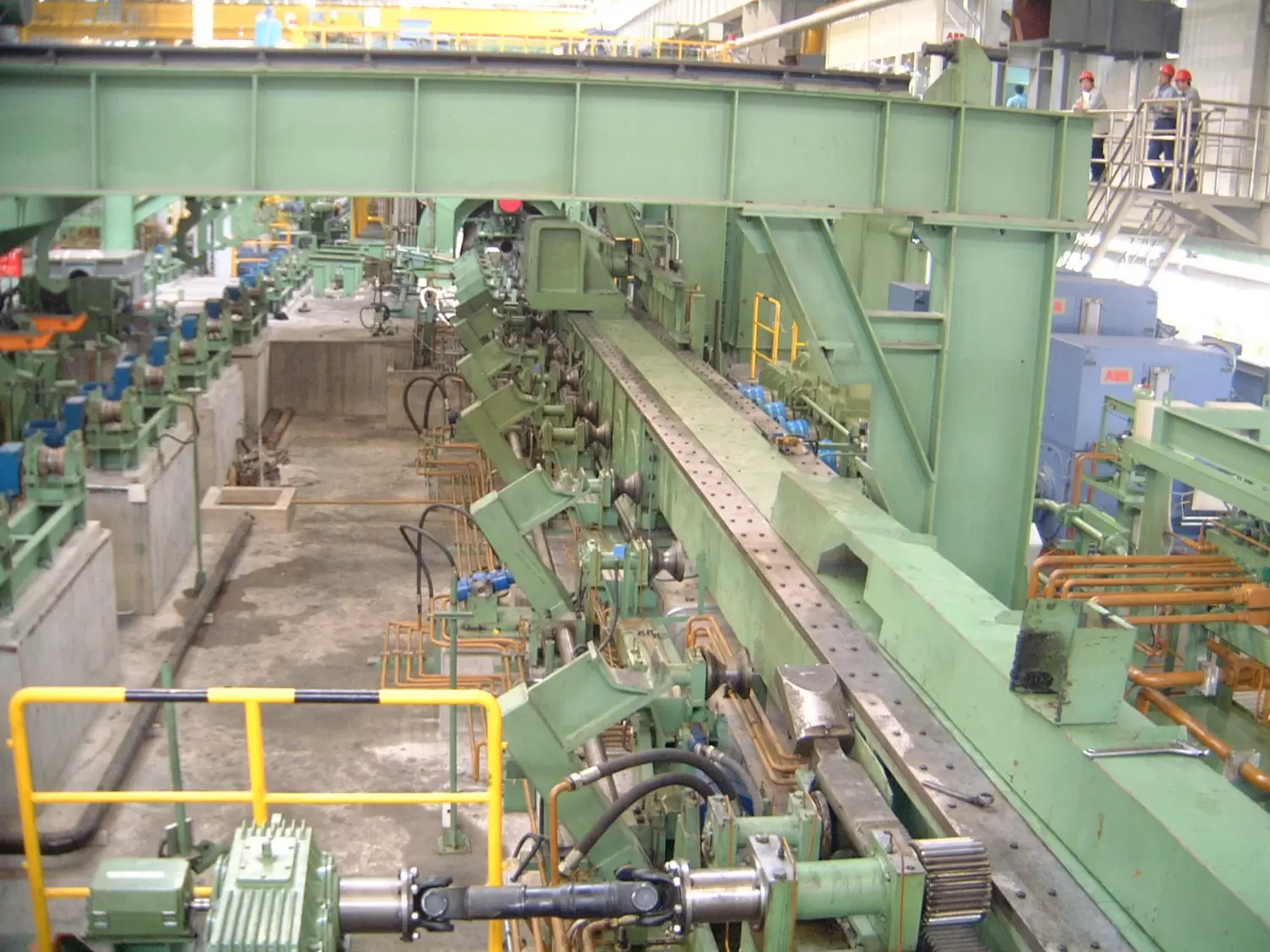
Our new generation of PQF® plants represents a really unique and highly attractive offer for tube manufacturers.
With regard to new plants, the investment in a fourth-generation PQF® remains the same. Additional investments are only required for some equipment areas in the line, because furnace and saw capacities, for example, need to be increased. Even in the case of an upgrade, the financial outlays are manageable. These mainly concern adjustments to the cycle times and capacity extensions in the peripheral line equipment.
Thomas Maßmann, Executive Vice President Long Products at SMS group: \"We are convinced that our new generation of PQF® plants represents a really unique and highly attractive offer for tube manufacturers all over the world. Of course, the huge increase in capacity and productivity also ensures a faster return on investment. Our team is on hand to present the technological innovations and the economic benefits to plant owners and interested parties. We are very well equipped for personal online and video conference presentations or, wherever possible, for meetings on site in compliance with all current hygiene regulations.\"
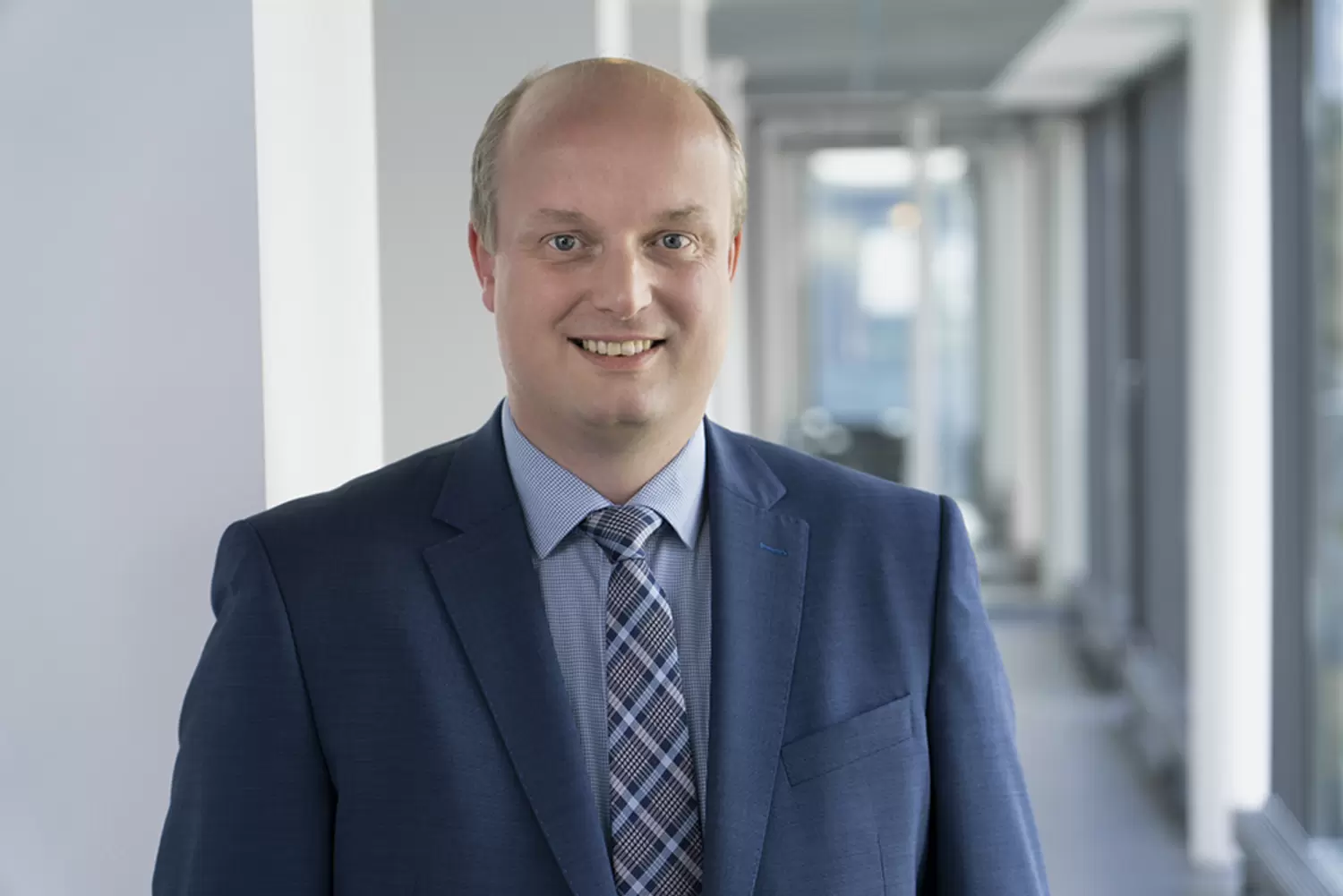