On the banks of the Mississippi in Arkansas, USA, Big River Steel operates North America's newest and greenest steelmaking plant. The plant has an annual capacity of 1.5 million tons which currently is increased to 3 million t/year in a second construction phase. The product range includes strips made of silicon steels, high-strength AHSS grades for the automotive industry and high-strength tube grades for oil and gas field pipelines and for transport pipelines.
Project
SMS group supplied all the plants for the new steel complex, including the mechanical equipment as well as all the electrical and automation systems. For the first construction stage, SMS supplied a gas cleaning plant, a 150-t electric arc furnace, a 150-t twin-ladle furnace, and a 150-t RH circulation degasser. Downstream equipment consists of a six-stand CSP® plant, a pickling line / tandem cold mill (PLTCM), an offline skin-passing mill (SPM), batch annealing furnaces, and a universal annealing and hot-dip galvanizing line (CAL/CGL).
SMS group email service
Our promise to you: this is not just another newsletter!
Use our contact form for questions, inquiries or personal contact.
Digitalization
Big River Steel is the world's first "Learning steel plant". It continually optimizes the production process from the raw material all the way down to the finished product as part of an integrated supply chain. This is achieved by the use of process know-how and expertise as well as physical and data-controlled models.
Electrical and automation systems
SMS group equipped all the plants at Big River Steel with X-Pact® electrics and automation. This included a flexible production planning system, the technological process models, the highly dynamic technological controls and sequence controls, the integrated and user friendly operation and visualization systems, the technological measuring devices and sensors, the power distribution and the main and auxiliary drives.
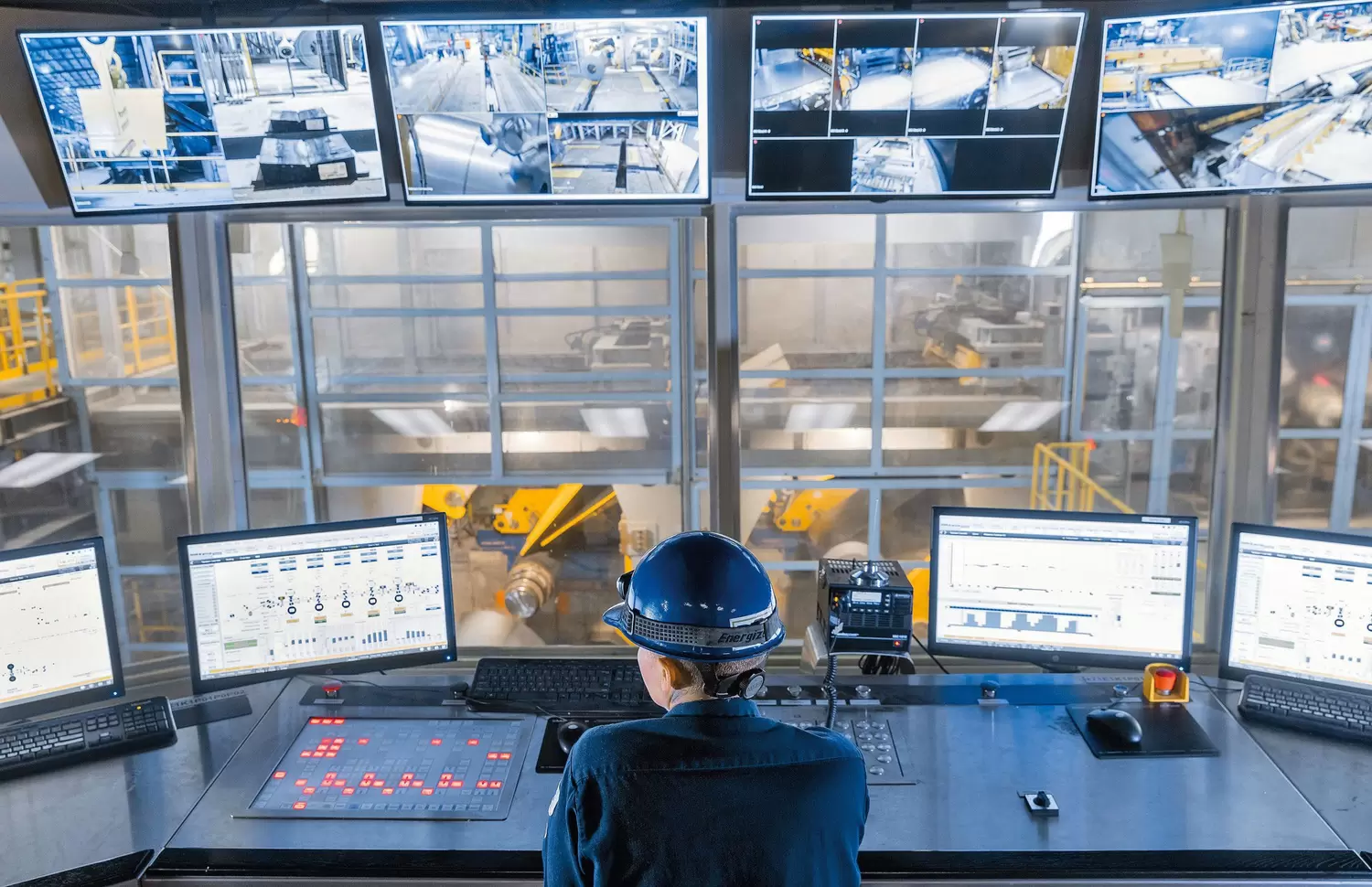
Service first
SMS group offers full-service package for North America’s most modern steel mill.
SMS Technical Services (STS) has opened a new maintenance shop, only two miles away from the Big River Steel’s plant. STS performs all maintenance services on the continuous caster, on the molds, and the segments and rolling mill components for the CSP®-plant. In addition, SMS Technical Services is responsible for two local roll shops of the hot and cold rolling mills. Altogether about 75 service employees are working in the workshop and the roll shops.
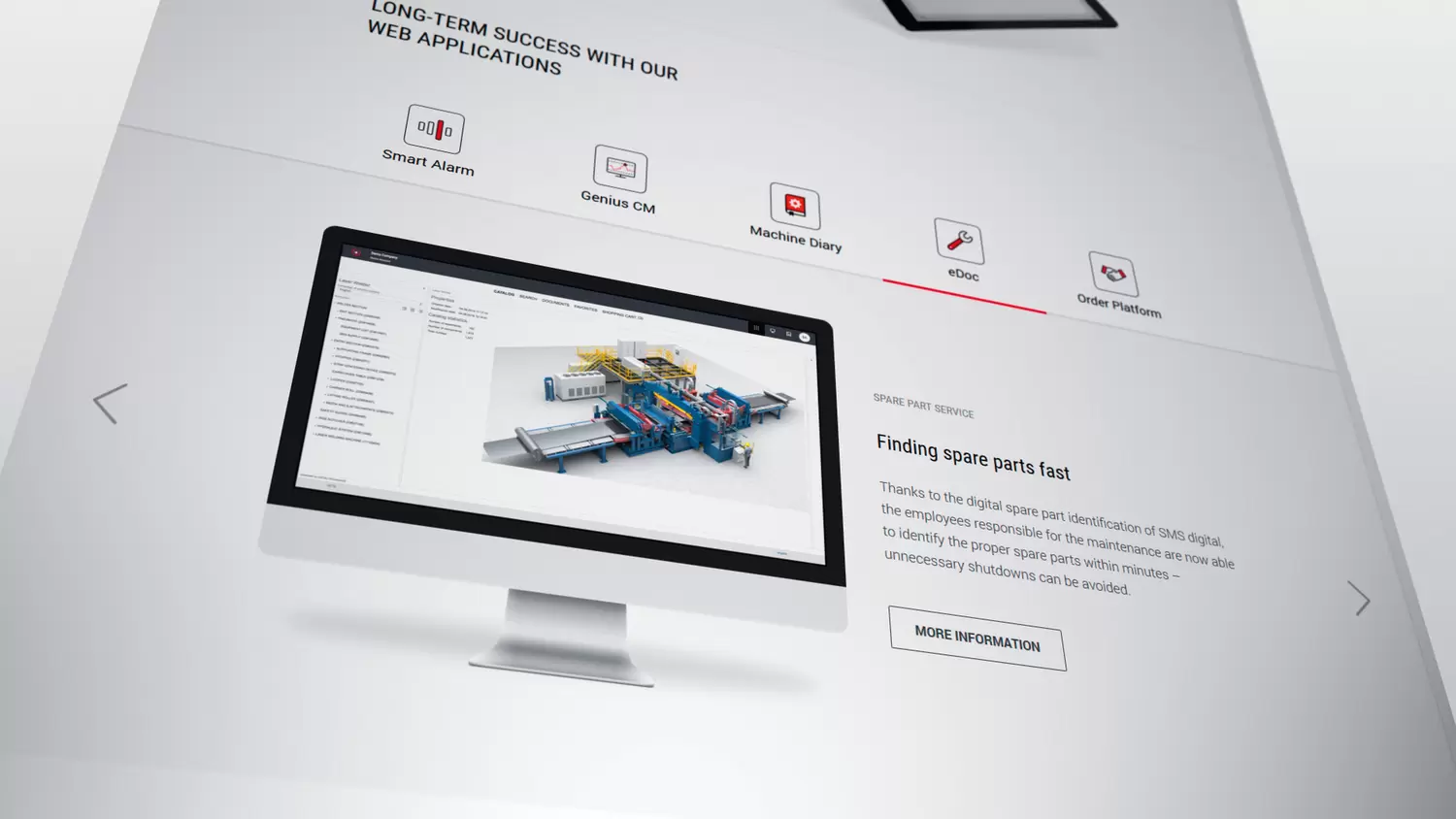
Big River Steel's view on the project
Six months after start of operation, Big River Steel executives tell their view on the project. They describe the partner-like relationship with the SMS group and address successes such as the steep ramp-up curve, the awards received for the eco-friendly plants and the solutions employed as part of the digitalization.