Comprehensive quality management
The SMS Quality Execution System® offers a comprehensive range of quality assurance tools, including predictive quality management, a unified data landscape across the production route, and rule-based quality and process assessment. The system allows users to gain valuable insights from data without requiring advanced data science skills, and it also helps maintain process stability. The QES® includes all kinds of decision-making support that is important for the operation of the plant and for the process chain.
Data from various automation levels is consolidated to represent each coil, bridging the gap between the physical and digital realms. This requires data to be transmitted flawlessly, enabling the virtual coil to mirror the physical coil. As the coil progresses through the production route, a digital counterpart is created at each stage of the process. The Quality Execution System (QES®) is designed to gather, combine, and examine all the data pertaining to a coil, thereby establishing the foundation for its digital twin.
By integrating all the data into the digital twin of each coil, steel manufacturers can achieve uninterrupted quality documentation and uncover latent quality opportunities.
Automatic product grading and release
Quality management remains a largely manual process in most rolling mills, even today. Plant personnel invest a great deal of time and effort into quality monitoring to pinpoint the exact cause of defects. The QES® technology offers an automated coil release process that facilitates quality monitoring, saving a significant amount of time and money. To do so, the software is equipped with customized rulesets for quality evaluation. That ruleset can be incorporated from existing quality evaluation tools. Additionally, the software offers methods to develop/adapt rules based on given processes and quality data. The automatic evaluation of product quality allows for automatic product quality approval and certification of every final product, freeing up resources for process and quality experts to focus on root cause analysis, continuous process and quality improvements, and quality assurance for critical products.
The 'AssignManager' application is a tool that helps ensure that produced coils meet the required specifications. It provides access to detailed information about the quality of the coils and helps identify alternative orders in case a finished product is not suitable for its original order. The application utilizes all available data to identify key parameters that drive quality performance. Web-based monitoring of key performance indicators enables re-assignments of products that correspond to the customer order.
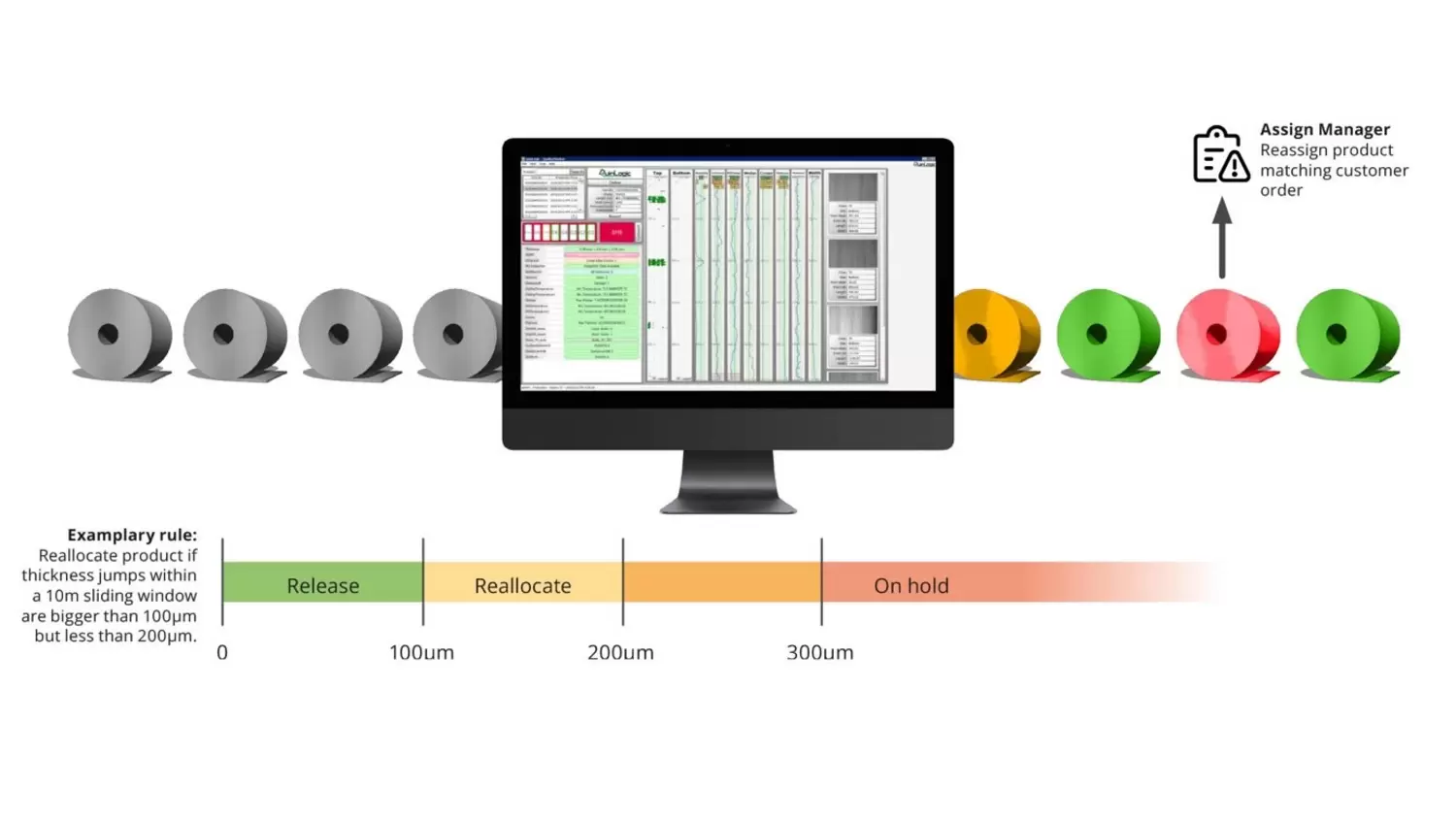
Enhanced with advanced applications
Within the QES®, the ‘Surface Quality Data Analysis’ application adds the visualization and evaluation of data from surface inspection systems, which often play a decisive role in the quality grading of coils. Today, data from over 90 inspection systems of all major brands can be processed and analyzed by the QES®. With the help of the software’s exceptional product genealogy, inspection results from any process step or manufacturer can be compared, and the development of defects can be tracked.
The ‘DataCorrelator’ is an integrated application that provides the user with an explorative data analysis tool. The primary focus is on conducting root cause analyses, comparative analyses, and building predictive models. This, combined with the user’s expertise, allows us to determine the influence of different factors on a variable and to compare variables under different conditions.
The ‘TrendMonitor’ uses data from the entire data pool and leverages it to monitor processes and product quality and keep these stable. Experts can observe how a process changes over time, identify trends, and recognize particular causes of variations. Statistical methods help to recognize process deviations automatically early on. Within TrendMonitor, data series can be defined based on the QES® product data model by selecting any context data for each data series by filtering, sorting, or grouping it.
The ‘Production Data Warehouse’ (PDW) provides secure, organized, and structured storage for data. Its rule-based data validation prevents errors from entering the system. Secure transactions prevent corrupt data from being stored, and extensive logging allows easy troubleshooting and verification. A unified data structure allows faster data access without compromising data integrity, regardless of the application used.
With the use of genealogical depictions and methodology, users can track the complete life cycle of a product from its inception to the final stage of quality check and shipment. This means that a complete family tree is recorded for each product. At any given point in time, it is possible to track the raw materials used and the processes applied to these materials to produce the final product for analysis.
QES® transformations at leading European steel and aluminum producers
Metal producers benefit significantly from implementing the QES®, appreciating the mature applications as well as the constant development and improvement of the system.
Speira, a leading European aluminum rolling and recycling company, is expanding the QES® application ‘Automatic Coil Grading & Release and Genealogy’ to two of its strip coating line routes as part of a long-term digitalization initiative it launched earlier. Speira’s aluminum rolling mill in Grevenbroich, Germany stands for high-quality automotive, beverage can, foil and lithographic products.
Speira started to automate the coil release system on its litho lines in 2011. The main driving force here was to improve the utilization of surface inspection data. Speira extended this upgrade to the new automotive line in 2018 and finally equipped all automotive lines with QES® and automated the quality grading for cans. Kai-Olav Runkel, Head of Quality Data and Systems & Central Support QA, says, “SMS group’s quality assurance solution supports us well in finding quality deviations quickly and setting the prerequisite for avoiding those in the future".
TATA Steel, the second largest European steel manufacturer, is also expanding cooperation with SMS as part of a long-term and early-started digitalization initiative. TATA started with their automated coil release at the cold mill in 2012. One of the main goals was to improve the utilization of surface inspection data and conduct post-processing. TATA invested in the automatic coil release for the DSP (direct sheet plant) and Hot Mill shortly after. The Cold Mill now started implementing the PDW part of the DataFactory. Wouter Overgaauw, Manager Quality Assurance Cold Rolling Mill Ijmuiden, states: “The amount of measurement data is steadily increasing, the possibilities for data-driven applications are improving, the PDW gives us the possibility to make better use of both data and applications.”