Market demands have changed over more than 30 years of plant operation and the market calls for a wider portfolio of alloys and grades. The maximum product width of about 800 millimeters at Golden Aluminum Inc. turned out to be a limiting factor. SMS group was the right technology partner for Golden Aluminum Inc. to systematically advance the potential of the strip casting facility to be able to even better meet modern market requirements. The nexcast® project strives for an increase in product width to 2,200 millimeters. This raises the minimill’s nominal capacity to about 200,000 tons per year and expands the range of grades that can be cast and rolled. To this end, extensive tests on process temperature management and surface quality have been performed at Golden Aluminum’s production plant in Colorado and also in SMS group’s test center in Hilchenbach, Germany.
Targeted advanced
Within the nexcast® project, SMS group engineers focus on design and technological advancements of the strip caster serving for controlled solidification of the liquid aluminum and for shaping it to hot strip. A particular challenge here is the increase in width. The new design solutions shall then be tested in further trials in the SMS test center. The nexcast® project will enable SMS group to expand its portfolio in the field of aluminum plants by a caster that can be combined, in interaction, with the proven hot rolling facilities to form a compact, continuously working process line for low to medium capacities.
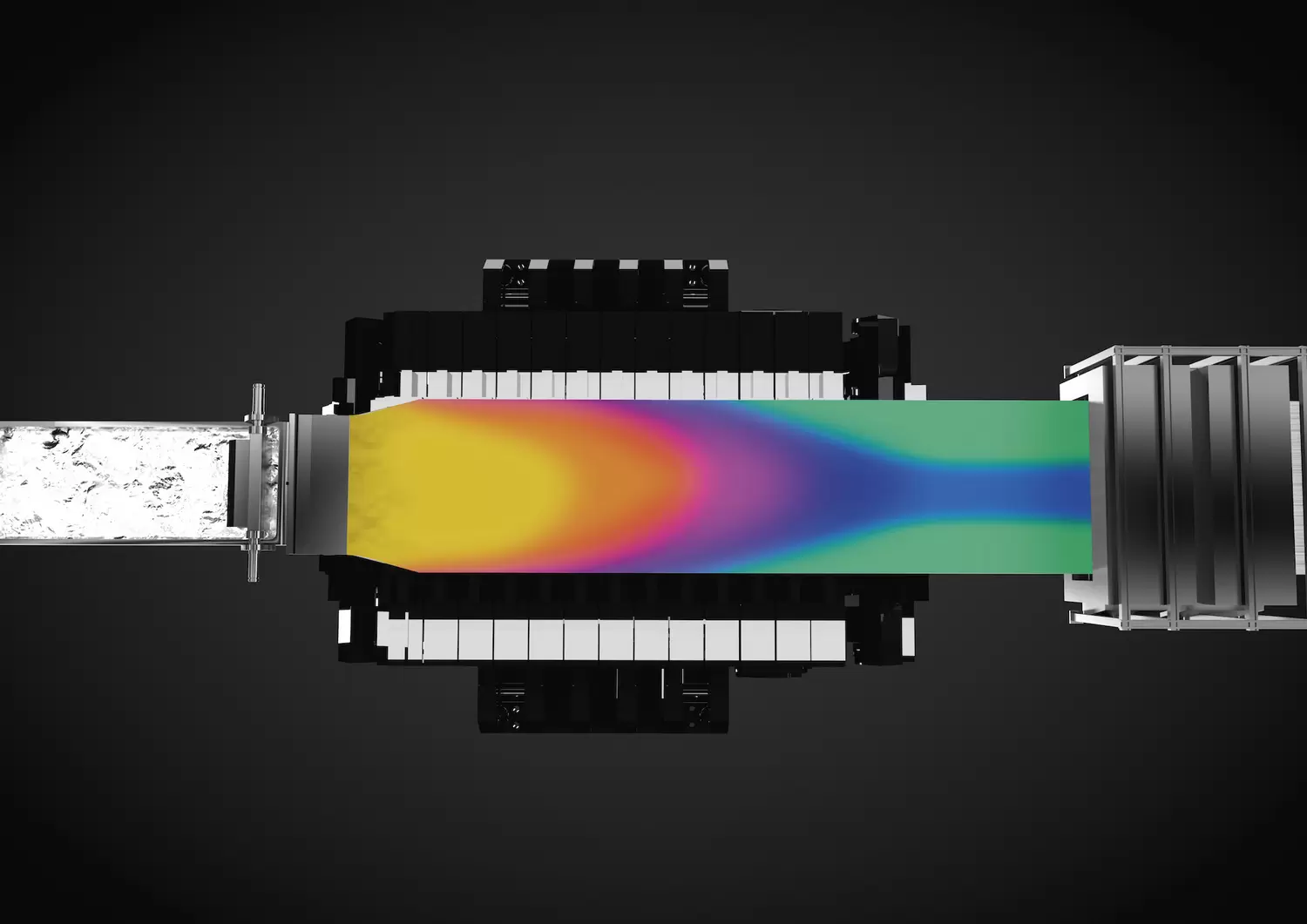
Features
- Wide range of alloys from AA1xxx to AA8xxx
- Annual output up to 200,000 tons
- Maximum strip width: 2,200 millimeters
- Reduced effort for material handling
- Significant reduction in investment and manufacturing costs due to compact plant configuration
NEXCAST® minimill
Similar to the CSP® technology that revolutionized the production of hot steel strip, the minimill concept for combined casting and rolling of aluminum strip has the potential to substantially enhance efficiency in aluminum production. Contrary to the conventional method, all steps needed to produce and process ingots are no longer required. This means that sawing, grinding, heating and pre-rolling of Ingots can all be omitted. Since complete production plants are waived,investment cost savings of up to 40 percent are achievable for new facilities referred to a corresponding annual output. In addition, the compact production process reduces operating costs by up to 25 percent. The nexcast® minimill is particularly suited for businesses with low to medium production capacity and also for serving local market.